Concrete member and surface structure modeled in RFEM. The webinar in the link below demonstrates the design workflow according to the ACI 318-19 standard utilizing the RF-CONCRETE Members and Surfaces add-on modules.
5 star | ||
4 star | ||
3 star | ||
2 star | ||
1 star |
ACI 318-19 Concrete Structure
Number of Nodes | 88 |
Number of Lines | 130 |
Number of Members | 63 |
Number of Surfaces | 18 |
Number of Solids | 0 |
Number of Load Cases | 4 |
Number of Load Combinations | 13 |
Number of Result Combinations | 2 |
Total Weight | 593.812 tons |
Dimensions (Metric) | 30.500 x 15.088 x 15.088 m |
Dimensions (Imperial) | 100.07 x 49.5 x 49.5 feet |
You can download this structural model to use it for training purposes or for your projects. However, we do not assume any guarantee or liability for the accuracy or completeness of the model.





The material library already includes the American types of concrete and reinforcing steel available for design. However, you can always define other materials for the design according to ACI 318.
By default, the units that are used for the reinforced concrete design according to ACI 318 are set to the imperial system of measurement.

After the calculation, the module shows clearly arranged tables listing the deformation analysis results. All intermediate values are displayed in a comprehensible manner. Graphical representation of design ratios and deformation in RFEM allows a quick overview of critical areas.
Since the design results are displayed by surface or by point including all intermediate results, you can retrace all details of the calculation. The complete integration of results in the RFEM printout report guarantees verifiable structural design.
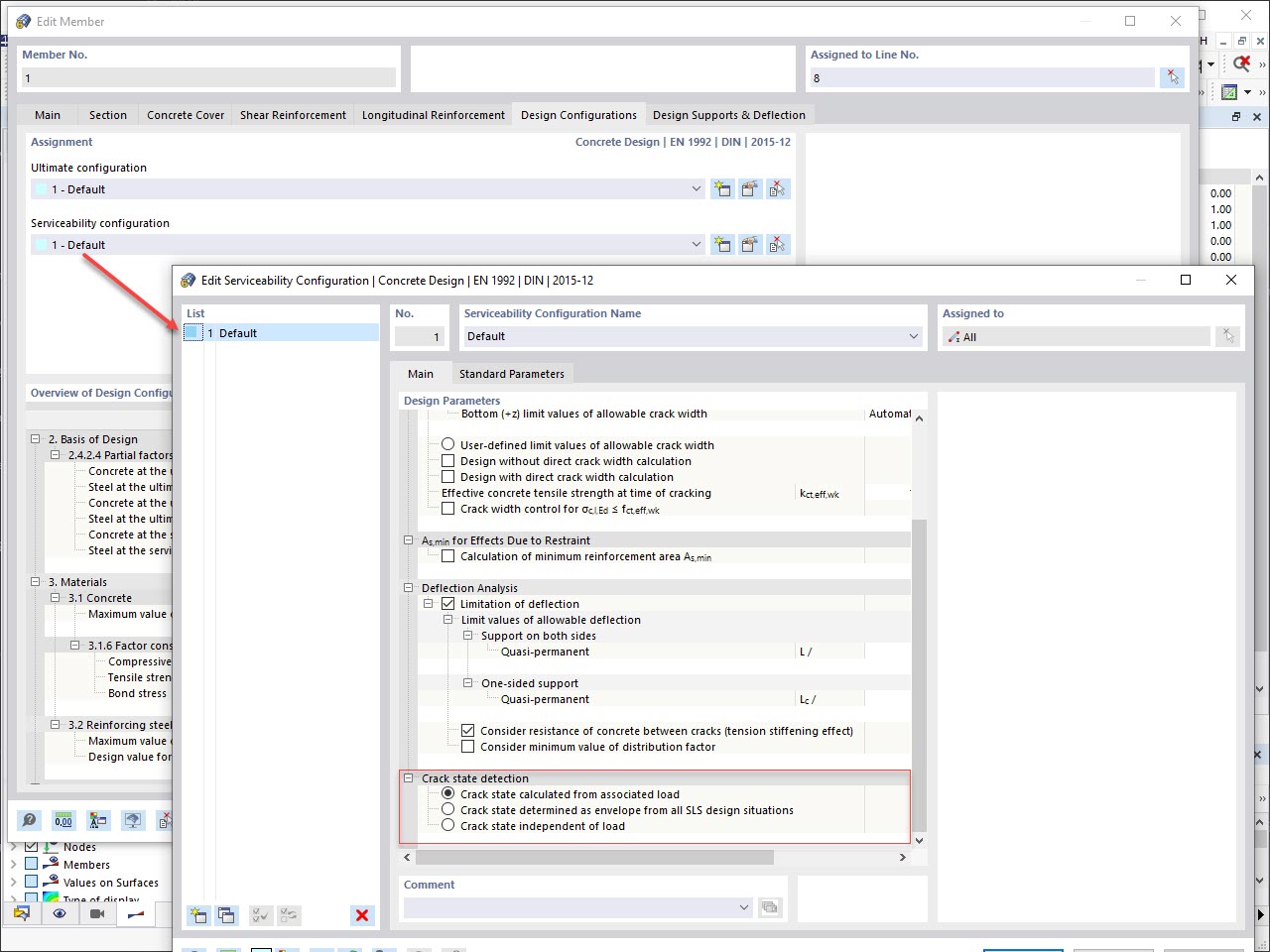
Various design parameters of the cross-sections can be adjusted in the serviceability limit state configuration. The applied cross-section condition for the deformation and crack width analysis can be controlled there.
For this, the following settings can be activated:
- Crack state calculated from associated load
- Crack state determined as an envelope from all SLS design situations
- Cracked state of cross-section - independent of load
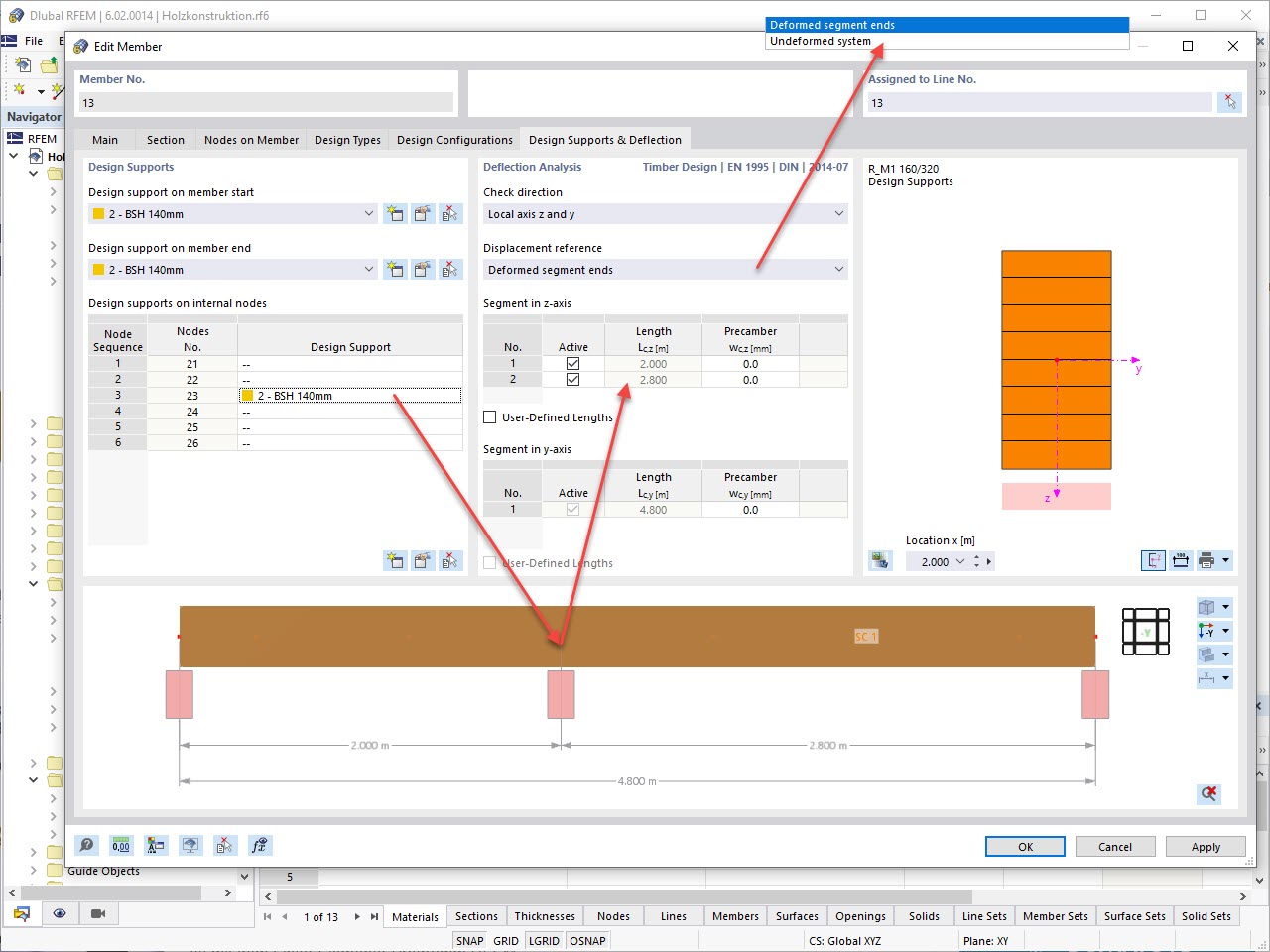
In the "Deflection and Design Support" tab under "Edit Member", the members can be clearly segmented using optimized input windows. Depending on the supports, the deformation limits for cantilever beams or single-span beams are used automatically.
By defining the design support in the corresponding direction at the member start, member end, and intermediate nodes, the program automatically recognizes the segments and segment lengths to which the allowable deformation is related. It also automatically detects whether it is a beam or a cantilever due to the defined design supports. The manual assignment, as in the previous versions (RFEM 5), is no longer necessary.
The "User-Defined Lengths" option allows you to modify the reference lengths in the table. The corresponding segment length is always used by default. If the reference length deviates from the segment length (for example, in the case of curved members), it can be adjusted.
Can I optimize parametric cross-sections?
How can I check the determination of the required reinforcement?
Is it possible to consider shear panels and rotational restraints in the global calculation?
How can I create a nodal constraint of the "Diaphragm" type in RFEM 6, as the function "1.31 – Nodal Constraints" from RFEM 5 is no longer available?