The RF-JOINTS Steel - Mast model combines the theoretical approaches of the large deformation analysis and enables a detailed design of steel towers. It particularly addresses the complex node connections and deformation processes. The precise simulation takes into account realistic load cases and shows innovative solutions. Ideal for use in demanding design scenarios.
5 star | ||
4 star | ||
3 star | ||
2 star | ||
1 star |
Steel Tower with Advanced Deformation Analysis
Number of Nodes | 157 |
Number of Lines | 366 |
Number of Members | 366 |
Number of Load Cases | 142 |
Number of Result Combinations | 1 |
Total Weight | 8,748 t |
Dimensions (Metric) | 5.109 x 5.109 x 30.098 m |
Dimensions (Imperial) | 16.76 x 16.76 x 98.75 feet |
Program Version | 5.02.00 |
You can download this structural model to use it for training purposes or for your projects. However, we do not assume any guarantee or liability for the accuracy or completeness of the model.
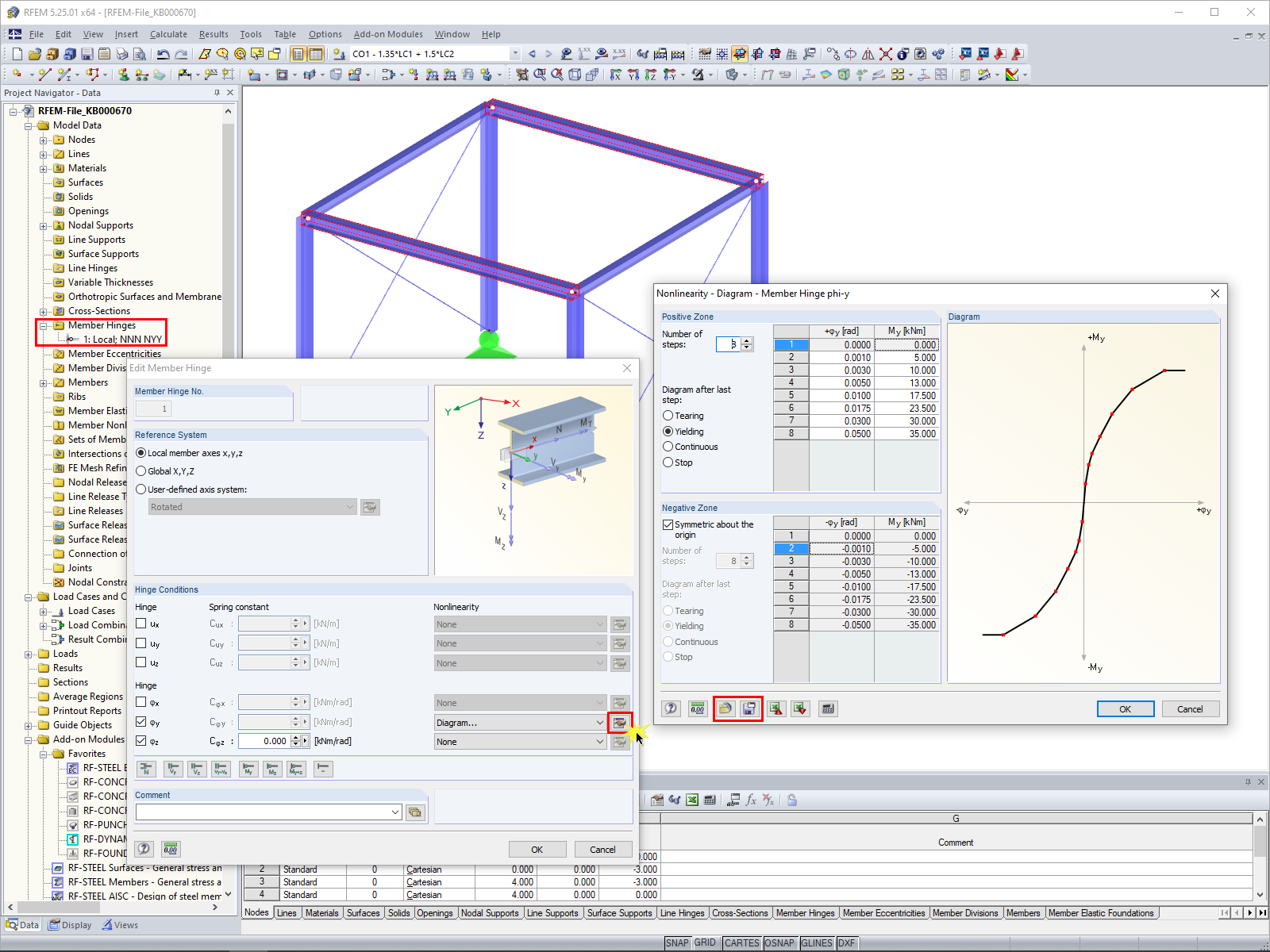
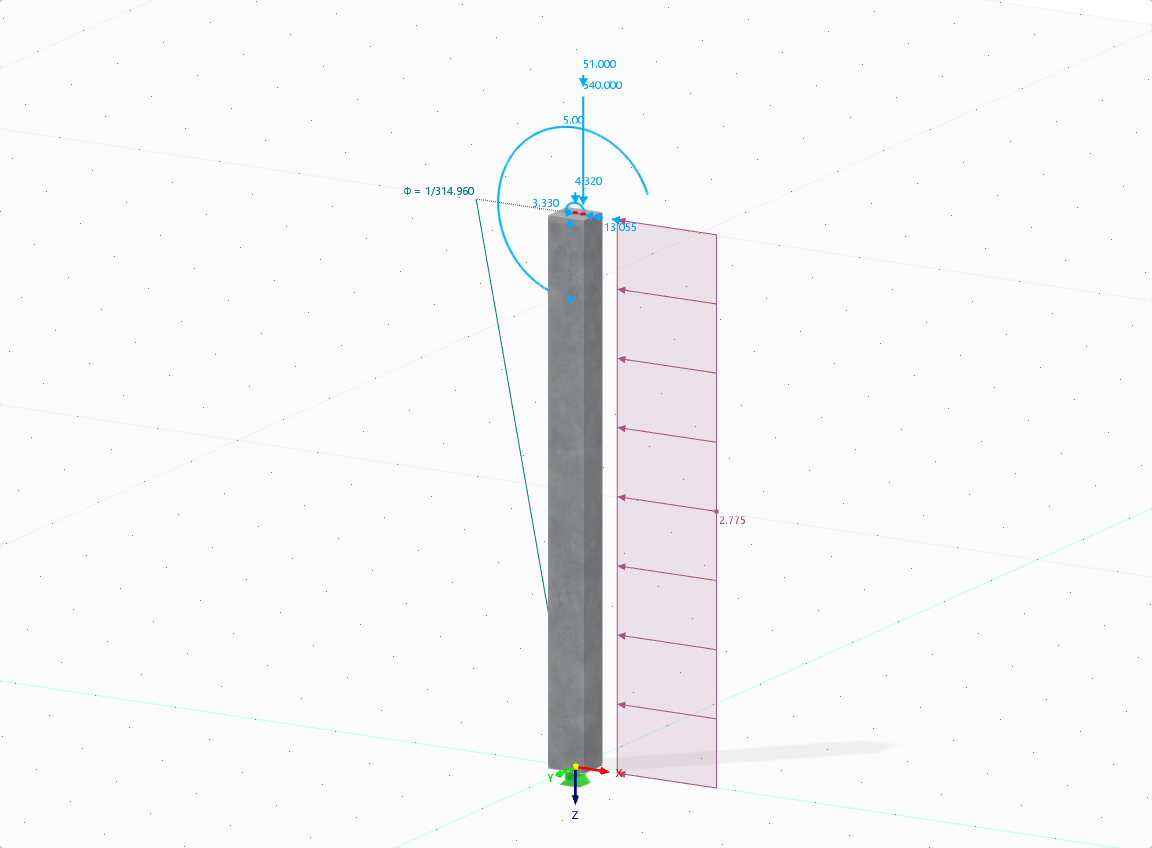
The aim of this technical article is to perform a design according to the general design method of Eurocode 2, using the example of a slender reinforced concrete column.

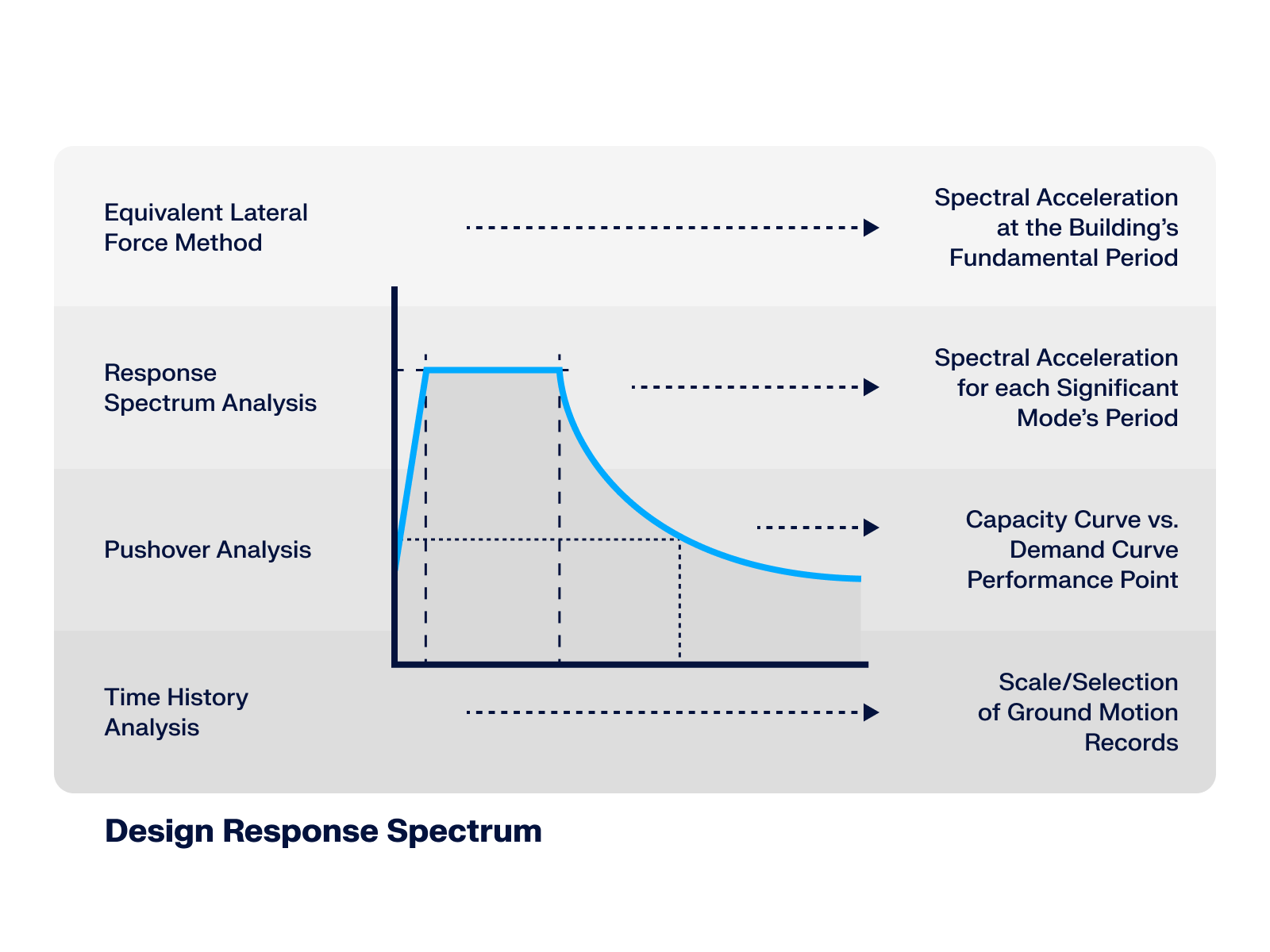
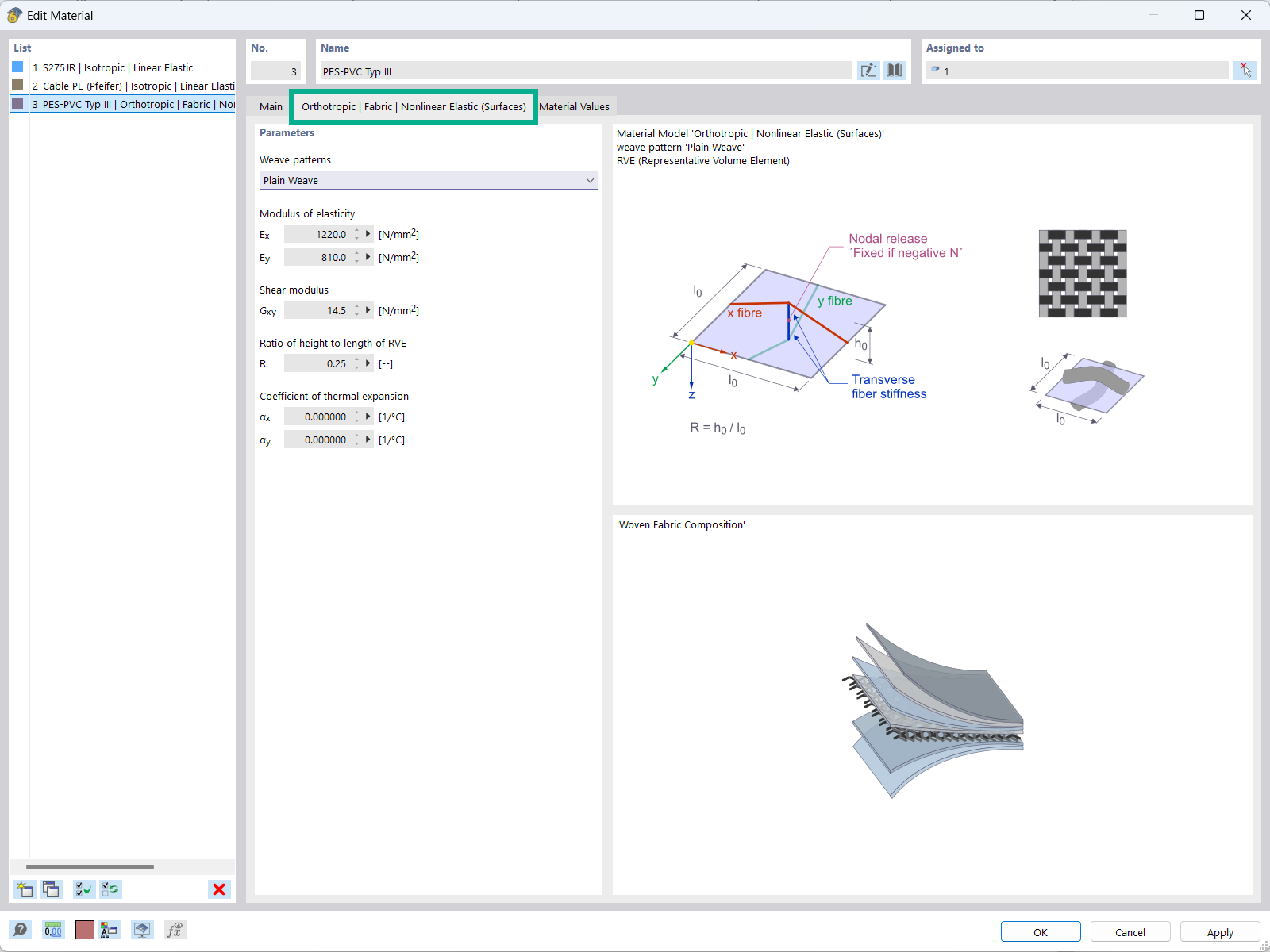
The "Orthotropic | Fabric | Nonlinear Elastic (Surfaces)" material model allows you to define prestressed fabric membranes using the representative microstructure-solid element model – RVE.
By considering the fabric geometry in the microstructure model, the corresponding transversal strain effect can now be considered for all force conditions in the membrane.
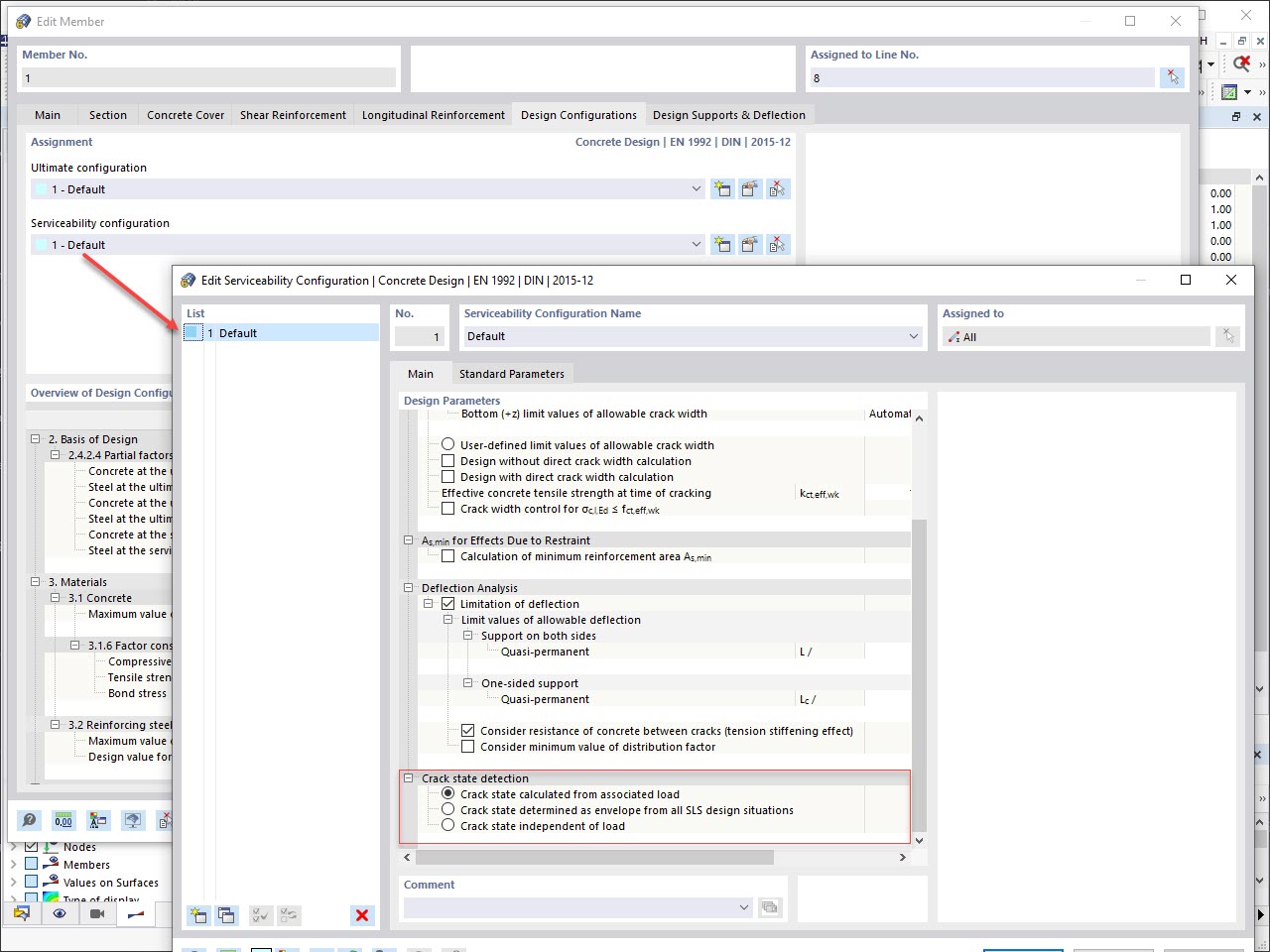
Various design parameters of the cross-sections can be adjusted in the serviceability limit state configuration. The applied cross-section condition for the deformation and crack width analysis can be controlled there.
For this, the following settings can be activated:
- Crack state calculated from associated load
- Crack state determined as an envelope from all SLS design situations
- Cracked state of cross-section - independent of load
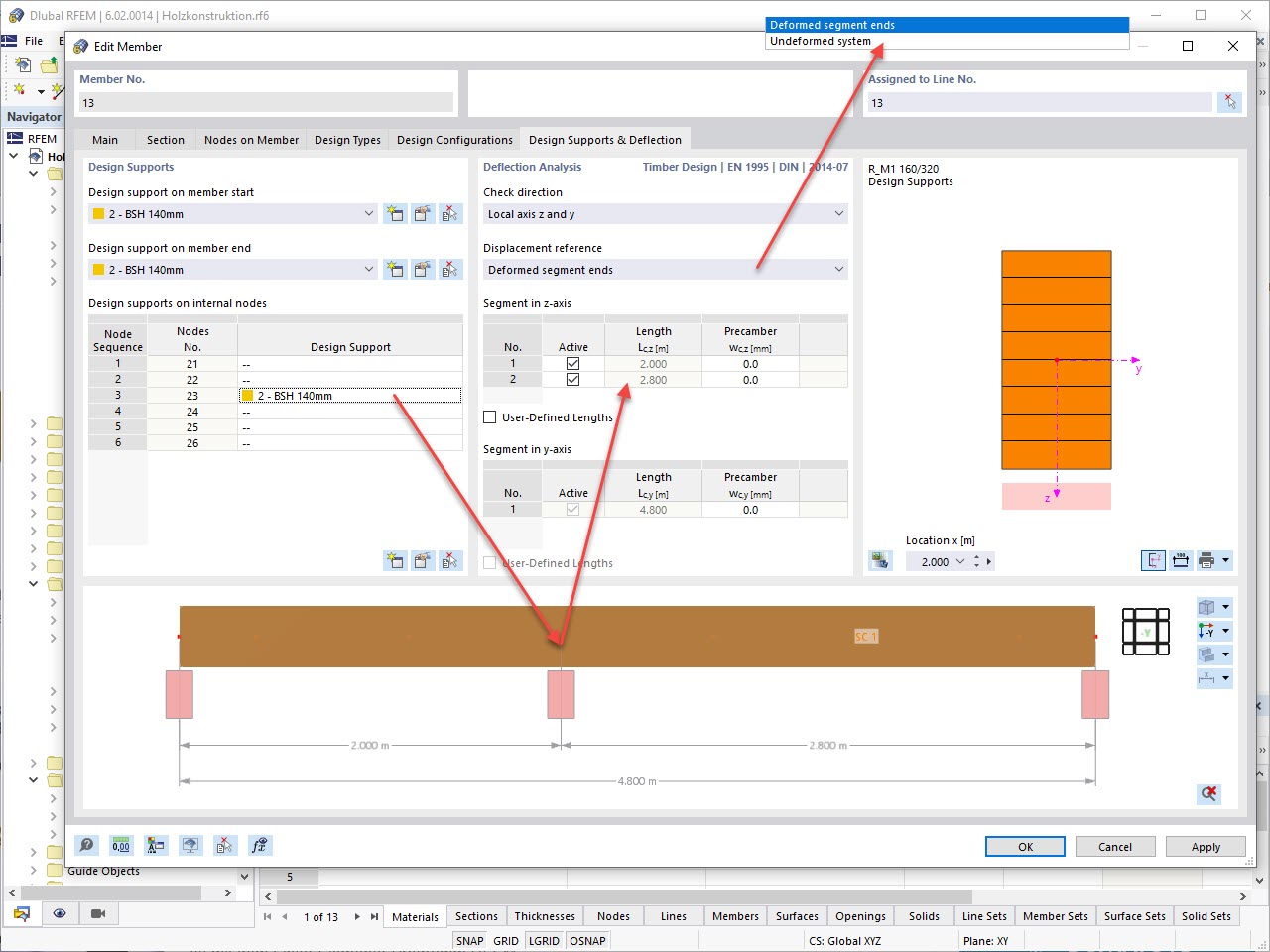
In the "Deflection and Design Support" tab under "Edit Member", the members can be clearly segmented using optimized input windows. Depending on the supports, the deformation limits for cantilever beams or single-span beams are used automatically.
By defining the design support in the corresponding direction at the member start, member end, and intermediate nodes, the program automatically recognizes the segments and segment lengths to which the allowable deformation is related. It also automatically detects whether it is a beam or a cantilever due to the defined design supports. The manual assignment, as in the previous versions (RFEM 5), is no longer necessary.
The "User-Defined Lengths" option allows you to modify the reference lengths in the table. The corresponding segment length is always used by default. If the reference length deviates from the segment length (for example, in the case of curved members), it can be adjusted.
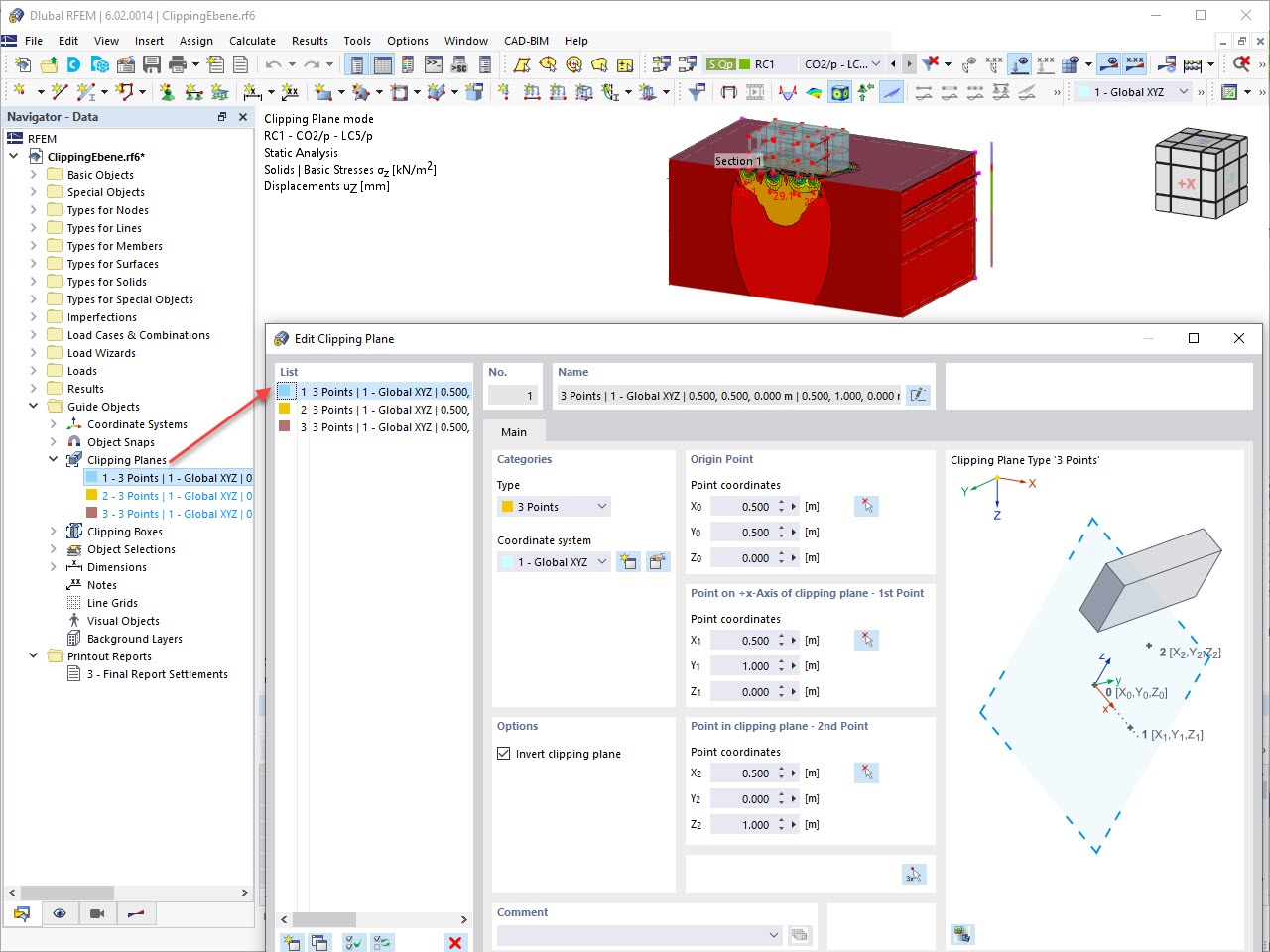
This feature also contributes to the clearly-arranged display of your results. Clipping planes are intersecting planes that you can place freely throughout the model. The zone in front of or behind the plane is consequently hidden in the display. This way, you can clearly and simply show the results in an intersection or a solid, for example.