This model presents how elastic compliance is taken into account in a timber connection and how the resulting torsional stiffness is recorded. The calculation is based on the slip modulus in order to model precise connection properties. It provides technical insights into the interaction between the slip modulus and stiffness. The practical simulation underlines the importance of optimized connection techniques.
5 star | ||
4 star | ||
3 star | ||
2 star | ||
1 star |
Model of Timber Connection: Elastic Slip Modulus and Rotational Spring Stiffness
Number of Nodes | 6 |
Number of Members | 4 |
Number of Load Cases | 2 |
Number of Load Combinations | 7 |
Number of Result Combinations | 4 |
Total Weight | 0,089 t |
Dimensions (Metric) | 2.467 x 0.467 x 3.234 m |
Dimensions (Imperial) | 8.09 x 1.53 x 10.61 feet |
Program Version | 8.25.01 |
You can download this structural model to use it for training purposes or for your projects. However, we do not assume any guarantee or liability for the accuracy or completeness of the model.
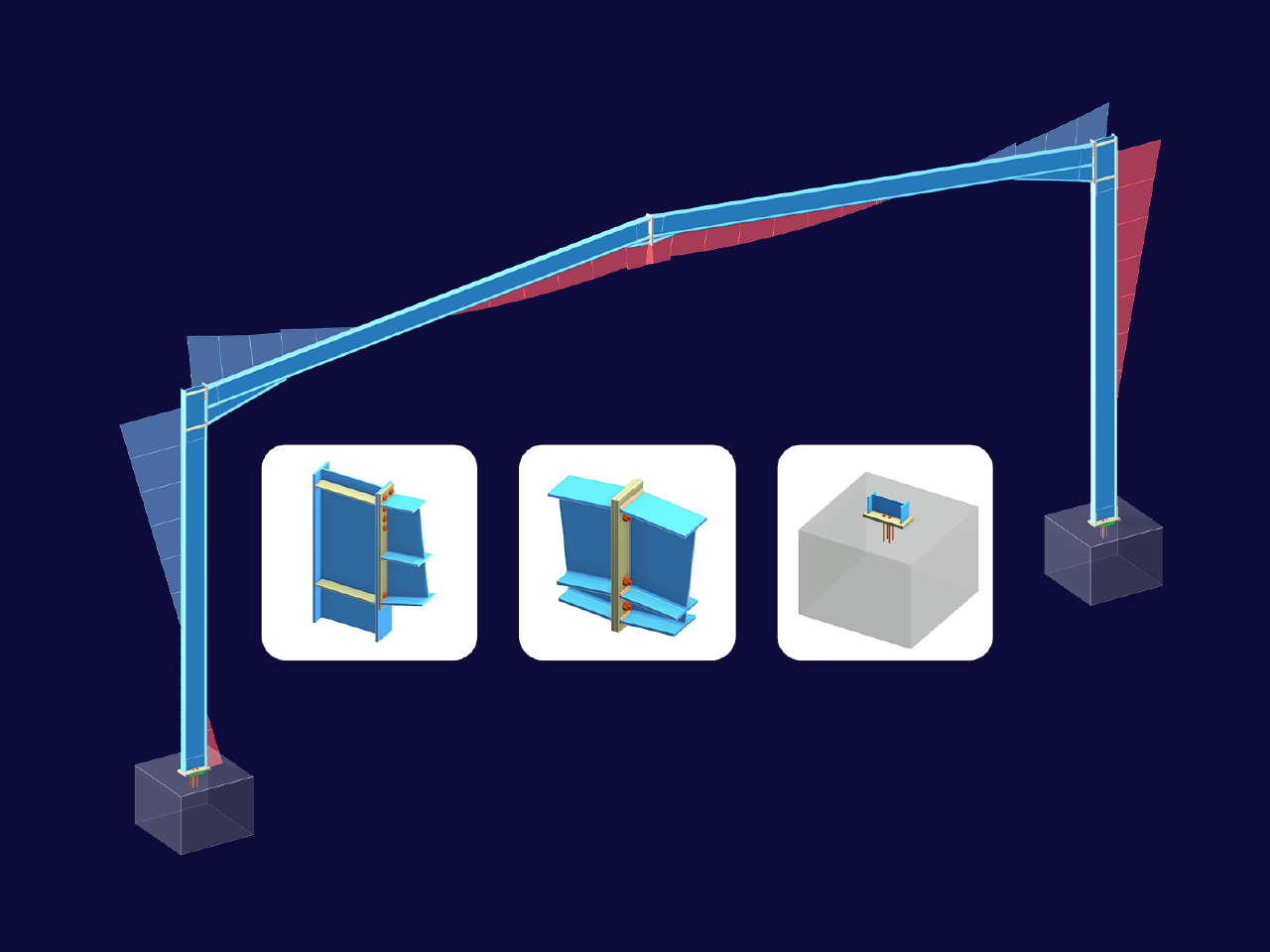
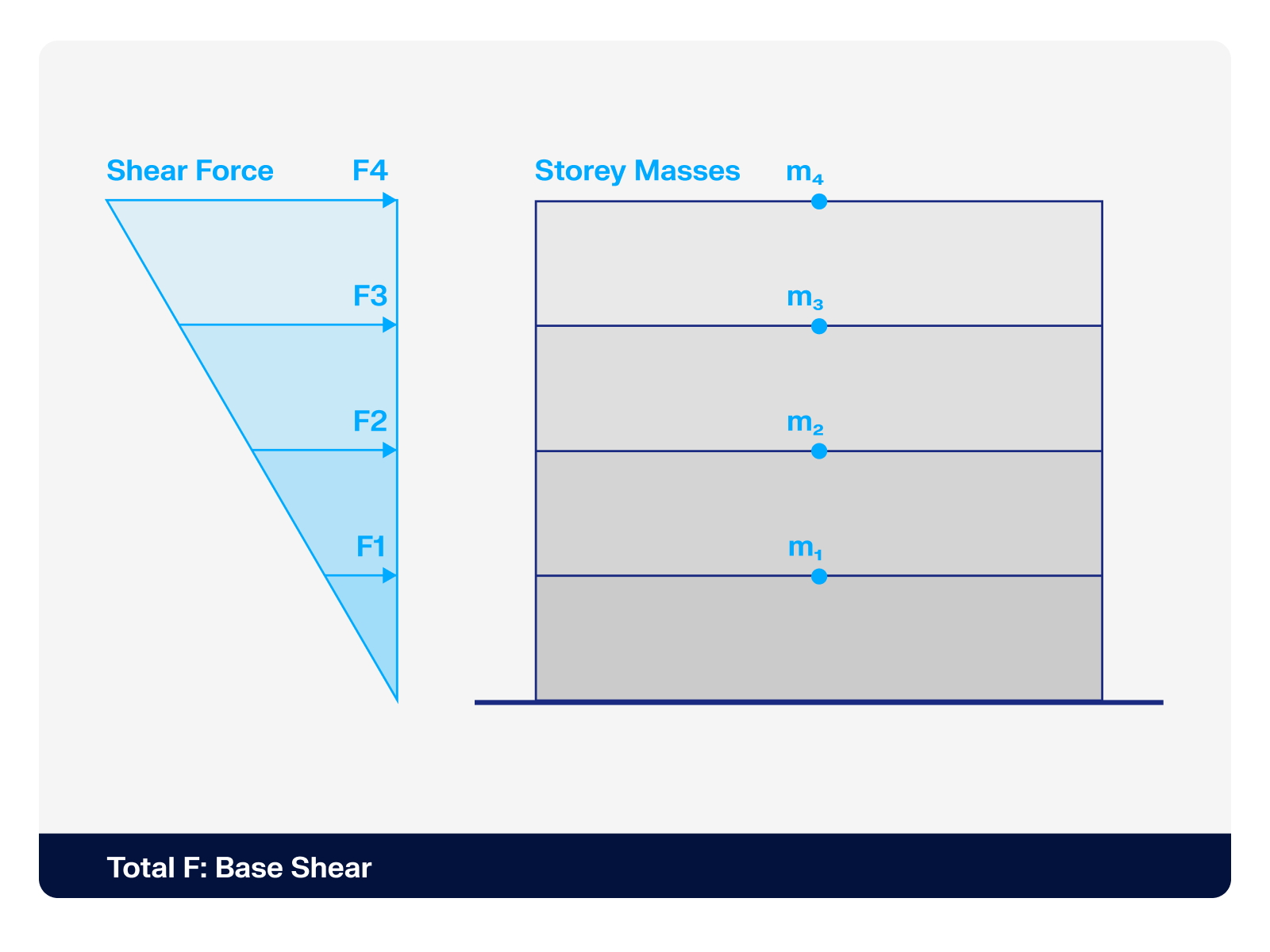.png?mw=512&hash=4a84cbc5b1eacf1afb4217e8e43c5cb50ed8d827)
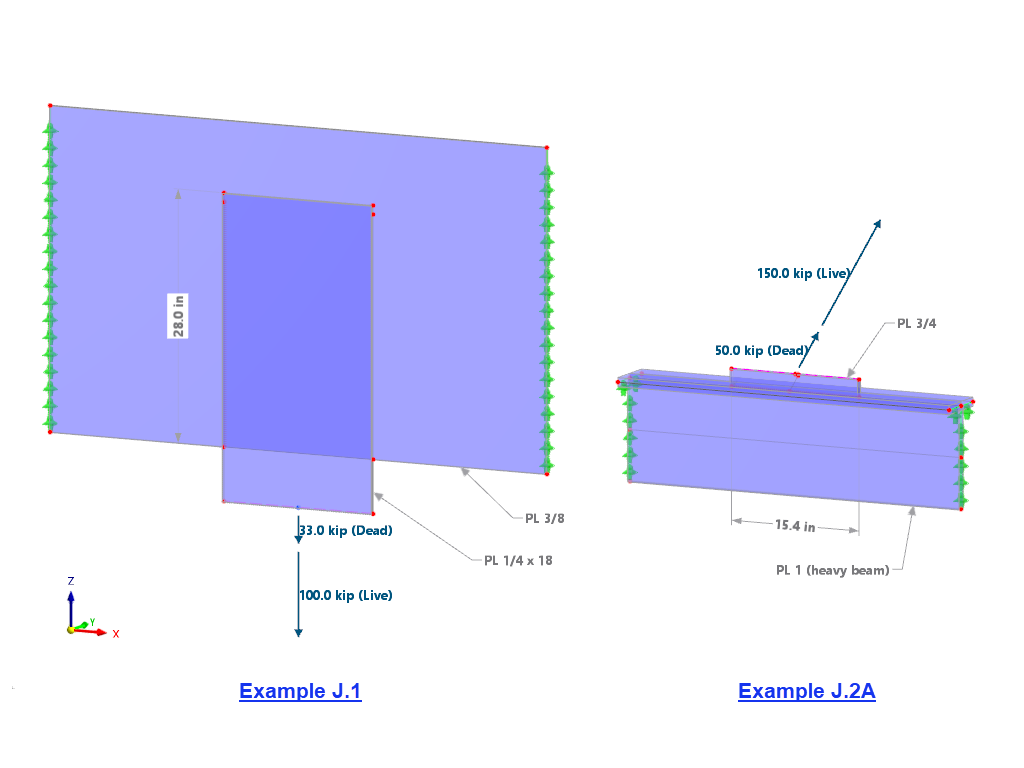
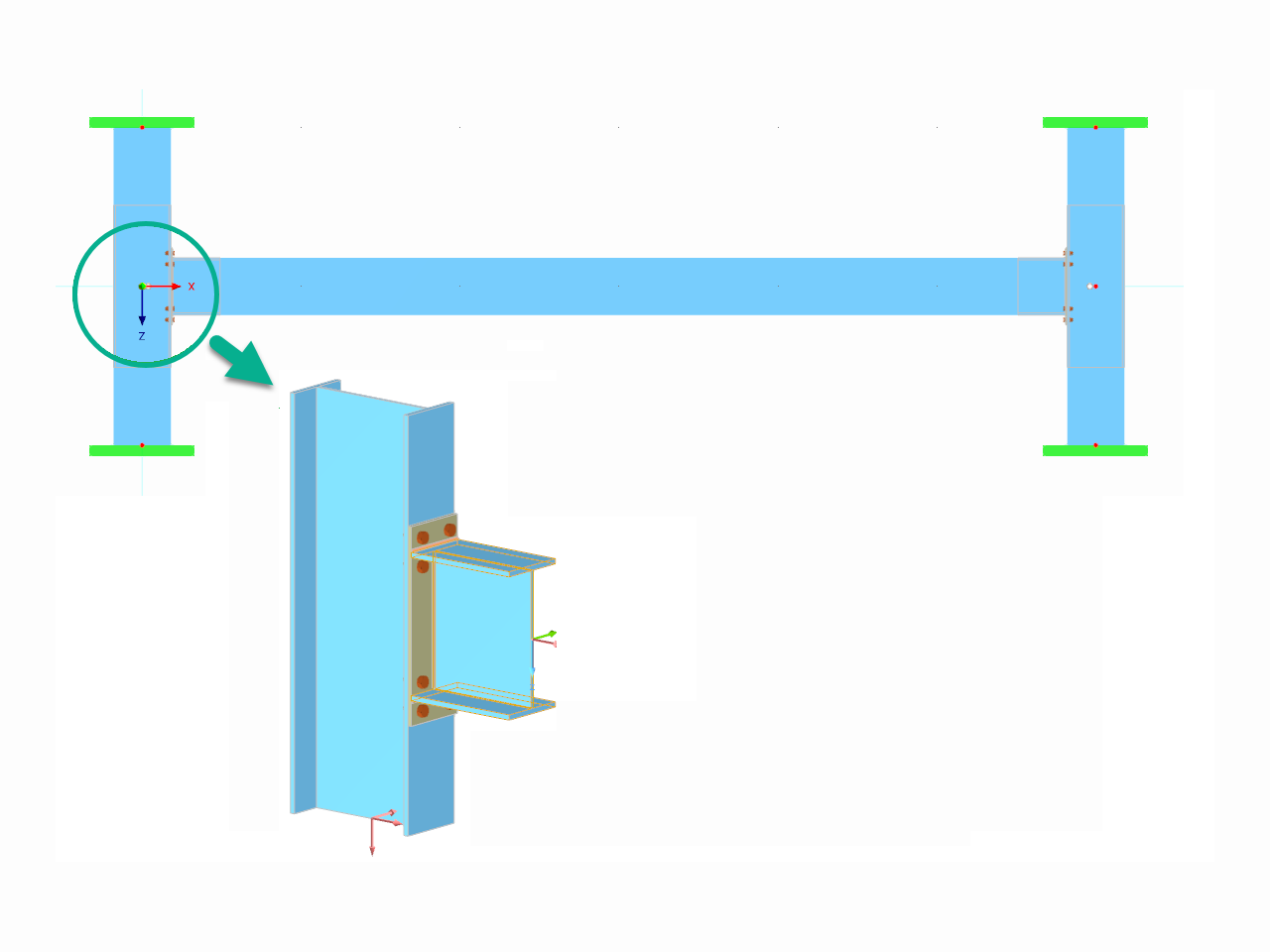
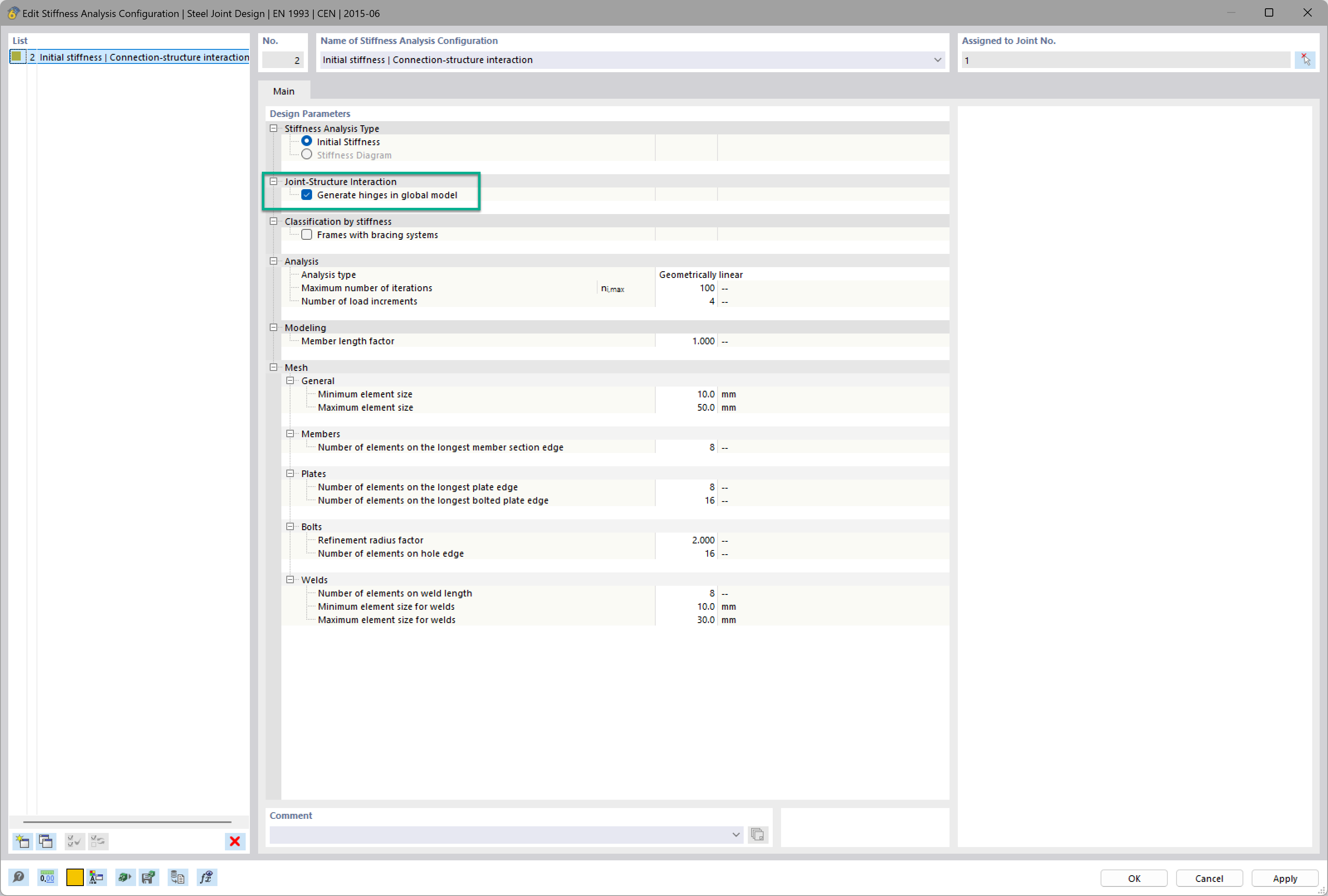
Want to automatically consider steel joint stiffness in your global RFEM model? Utilize the Steel Joints add-on!
Activate joint-structure interaction in the stiffness analysis of your steel joints. Hinges with springs are then automatically generated in the global model and included in subsequent calculations.
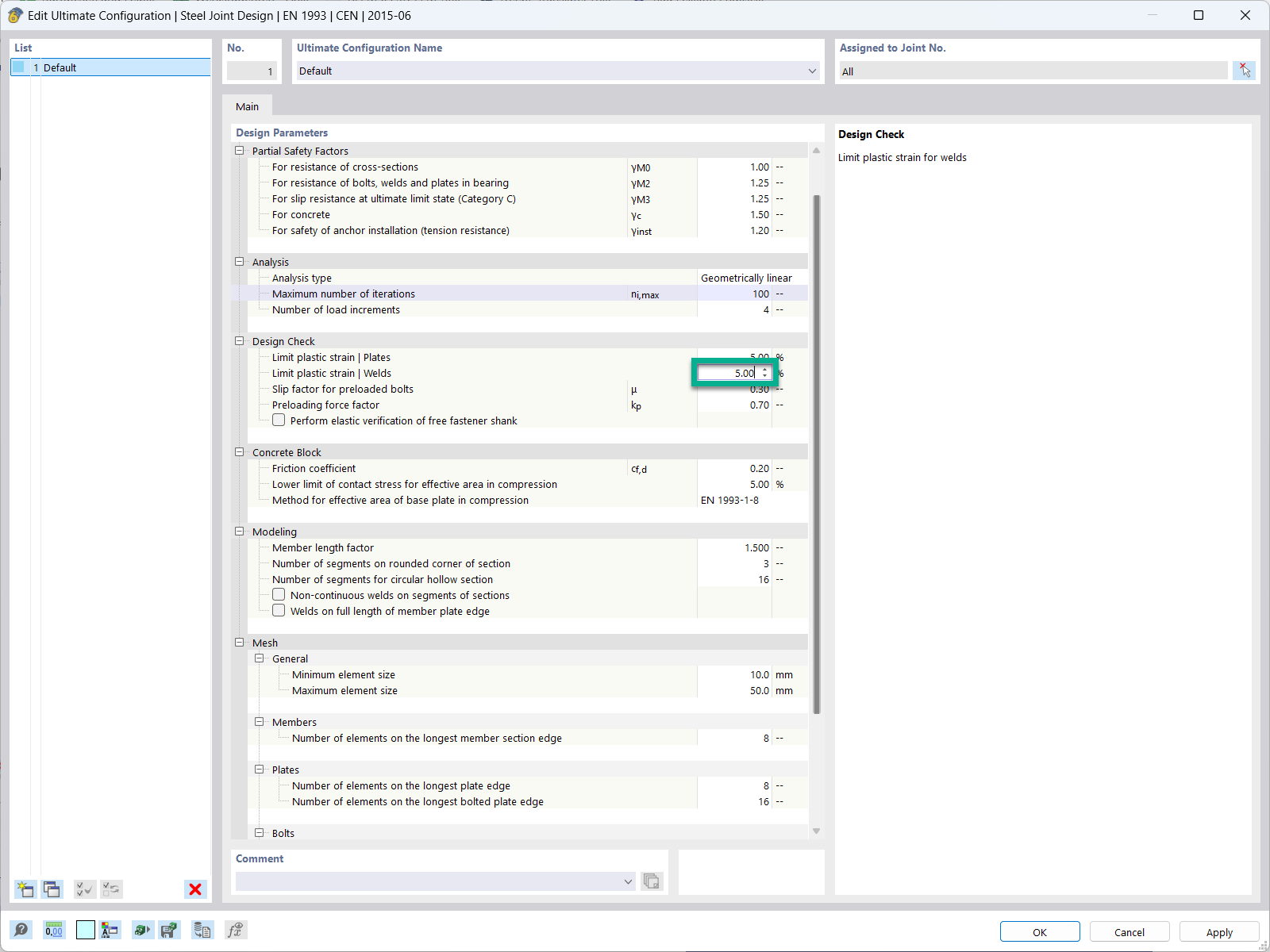
In the ultimate configuration of the steel joint design, you have the option to modify the limit plastic strain for welds.
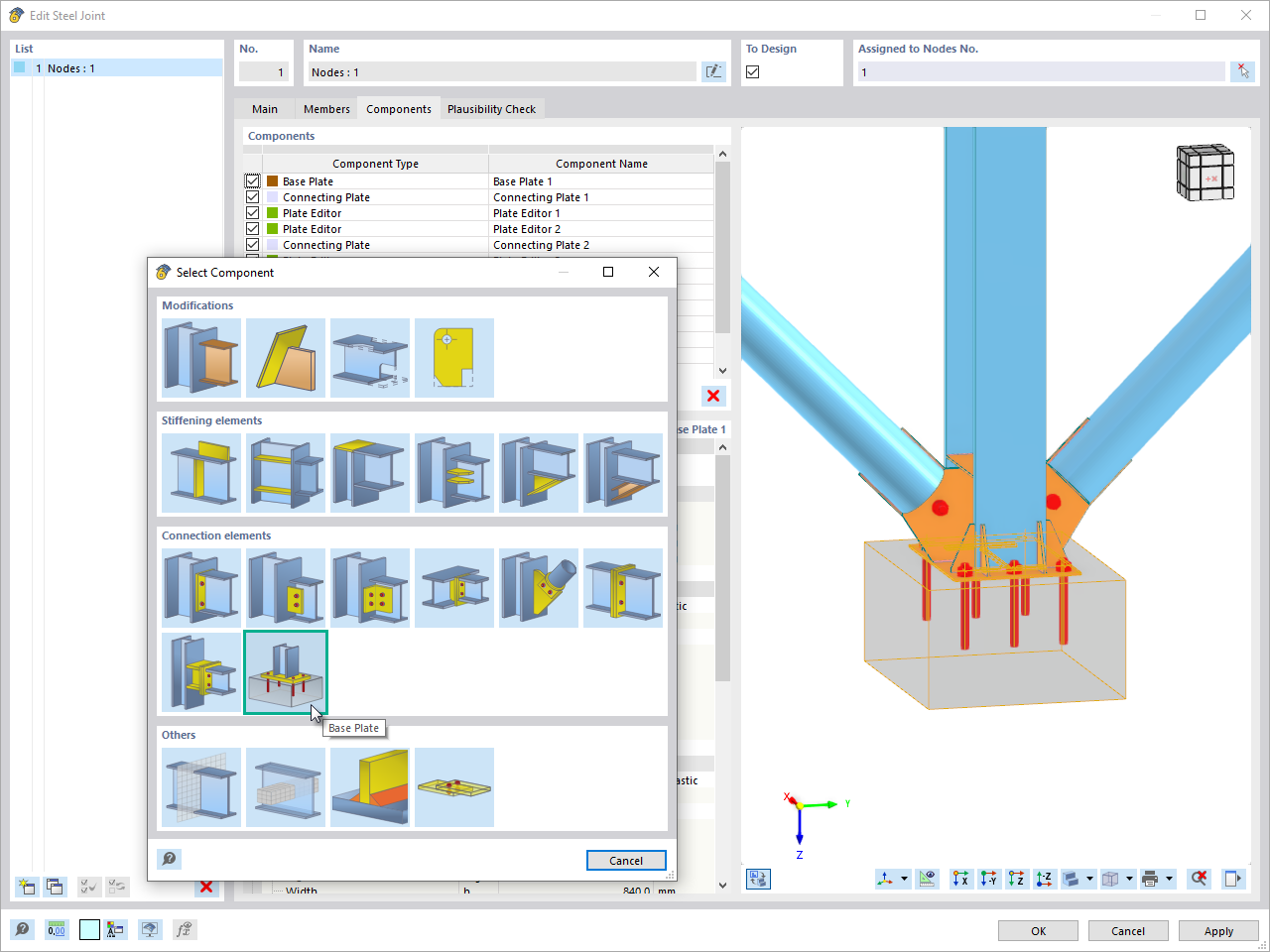
The "Base Plate" component allows you to design base plate connections with cast-in anchors. In this case, plates, welds, anchorages, and steel-concrete interaction are analyzed.
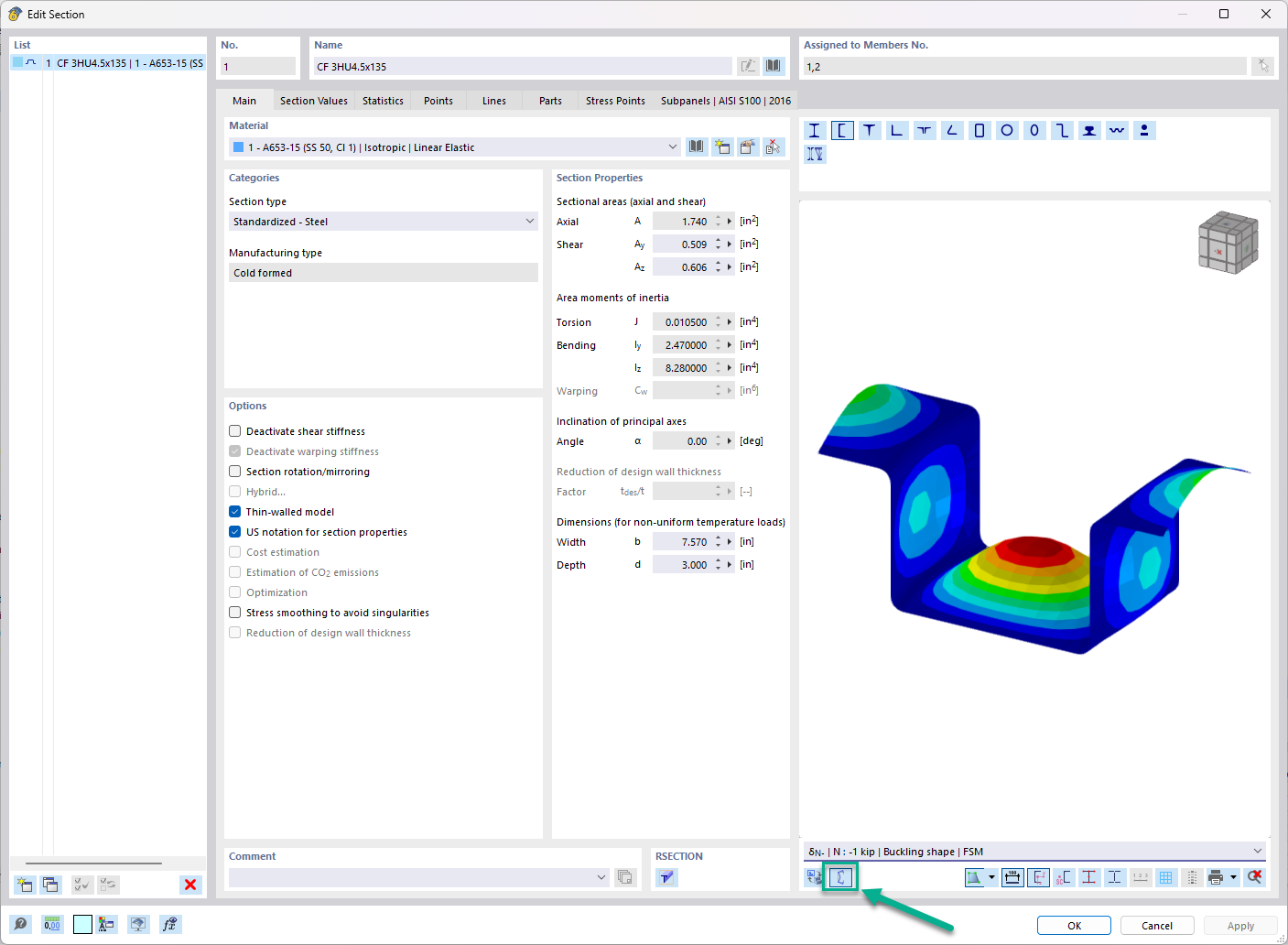
In the "Edit Section" dialog box, you can display the buckling shapes of the Finite Strip Method (FSM) as a 3D graphic.
In the Steel Joints add-on, I get high utilization ratios for preloaded bolts in the tension design. Where do these high utilization ratios come from and how can I evaluate the load-bearing reserves of the bolt?
How can treating a connection as fully rigid result in an uneconomical design?
Is it possible to consider shear panels and rotational restraints in the global calculation?