Here are some tips for an efficient and successful parameter model:
1. In order to avoid parametrization of intermediate nodes on lines, you can use the ‘Node on Line’ type. If partial lines between ‘nodes on line’ are required, you can additionally create lines on the line.
2. In the case of circles or arcs consisting of three points, it is necessary to parametrize all nodesindividually. You can avoid this by using the ‘Circle via Center and Radius’ type. It can be parameterized via the radius. If more segments on the circle are required, you can also use the ‘Node on Line’ type and thus create partial lines using the ‘Arc by Three Nodes’ type.
3. When using reference nodes, it is possible to move a whole point cloud via only one parameterized node. The points have to be entered solely as reference nodes of the desired node.
4. It is often useful to divide a large structure into individual elements to avoid parametrization of the entire structure. Then, the individual elements are saved as a block and the block parameters are adjusted during import. The advantage is that the parameters are lost after the import and therefore, you can modify the model only by deleting and reimporting the data.
5. Especially when creating many formulas that are the same due to large area, exporting to Excel (with the subsequent import to RFEM/RSTAB) can save a lot of time, because editing of the tables is even easier (formulas can be exported).
Tips for Parametrization
Mr. Günthel provides technical support for our customers.



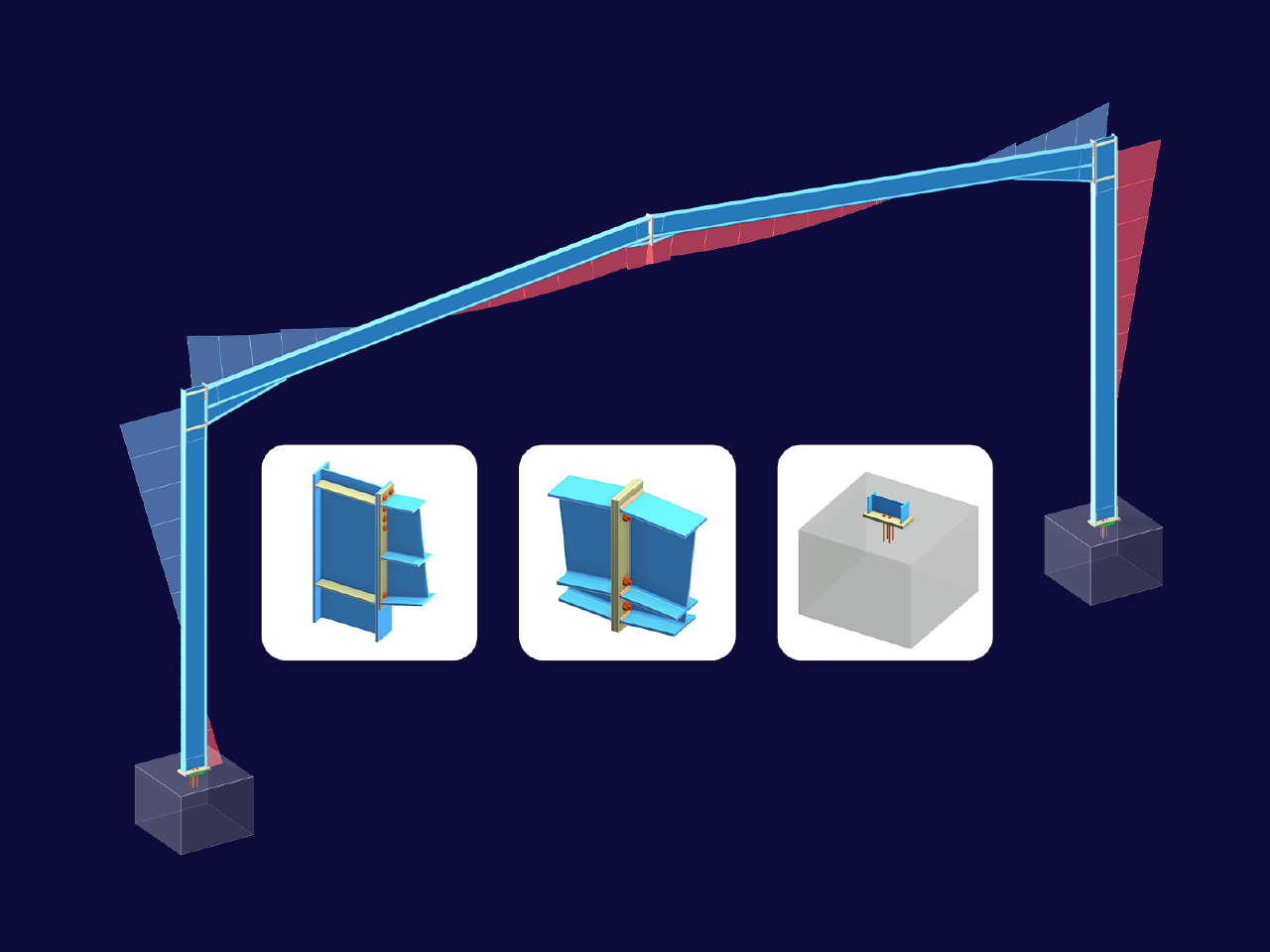
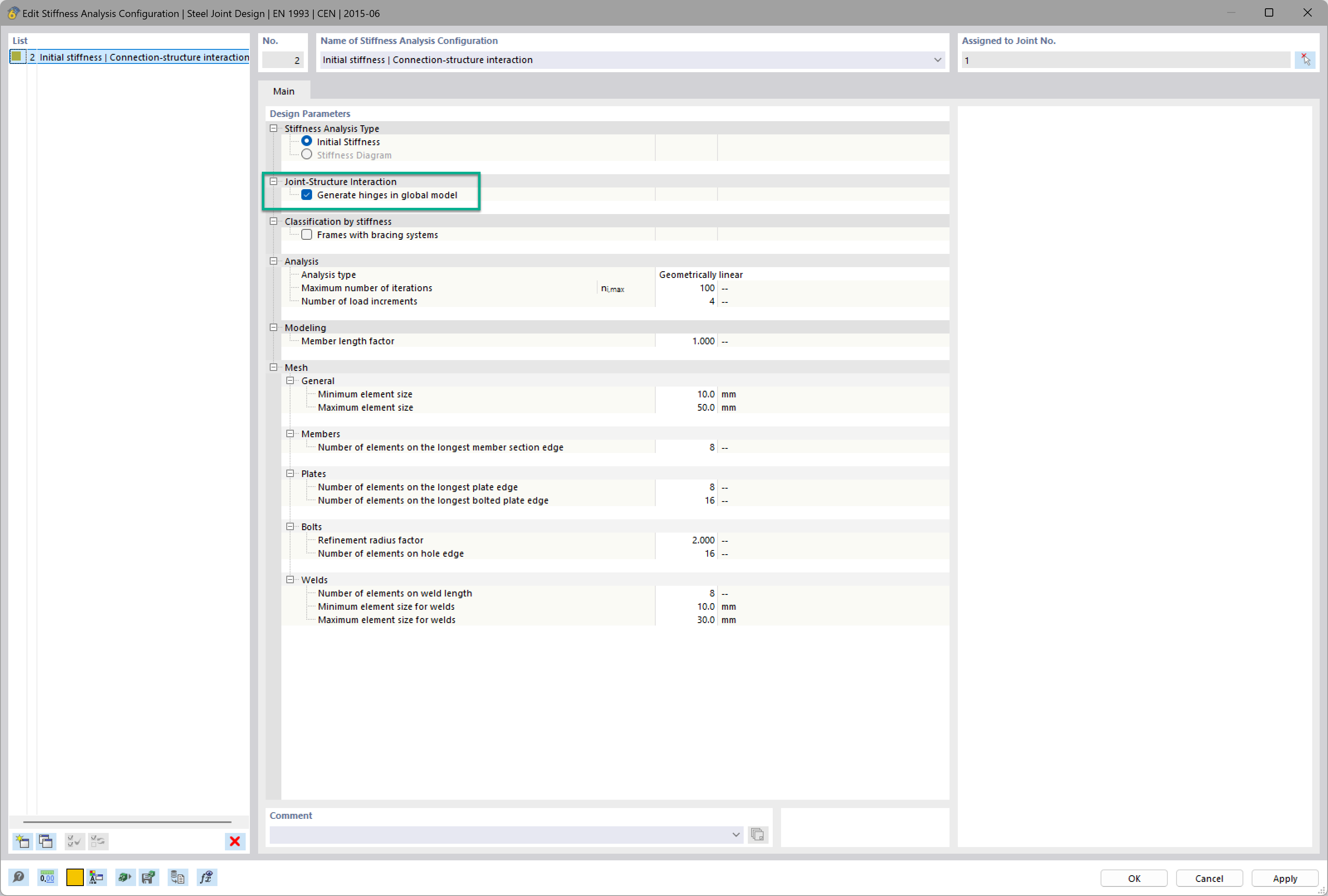
Want to automatically consider steel joint stiffness in your global RFEM model? Utilize the Steel Joints add-on!
Activate joint-structure interaction in the stiffness analysis of your steel joints. Hinges with springs are then automatically generated in the global model and included in subsequent calculations.
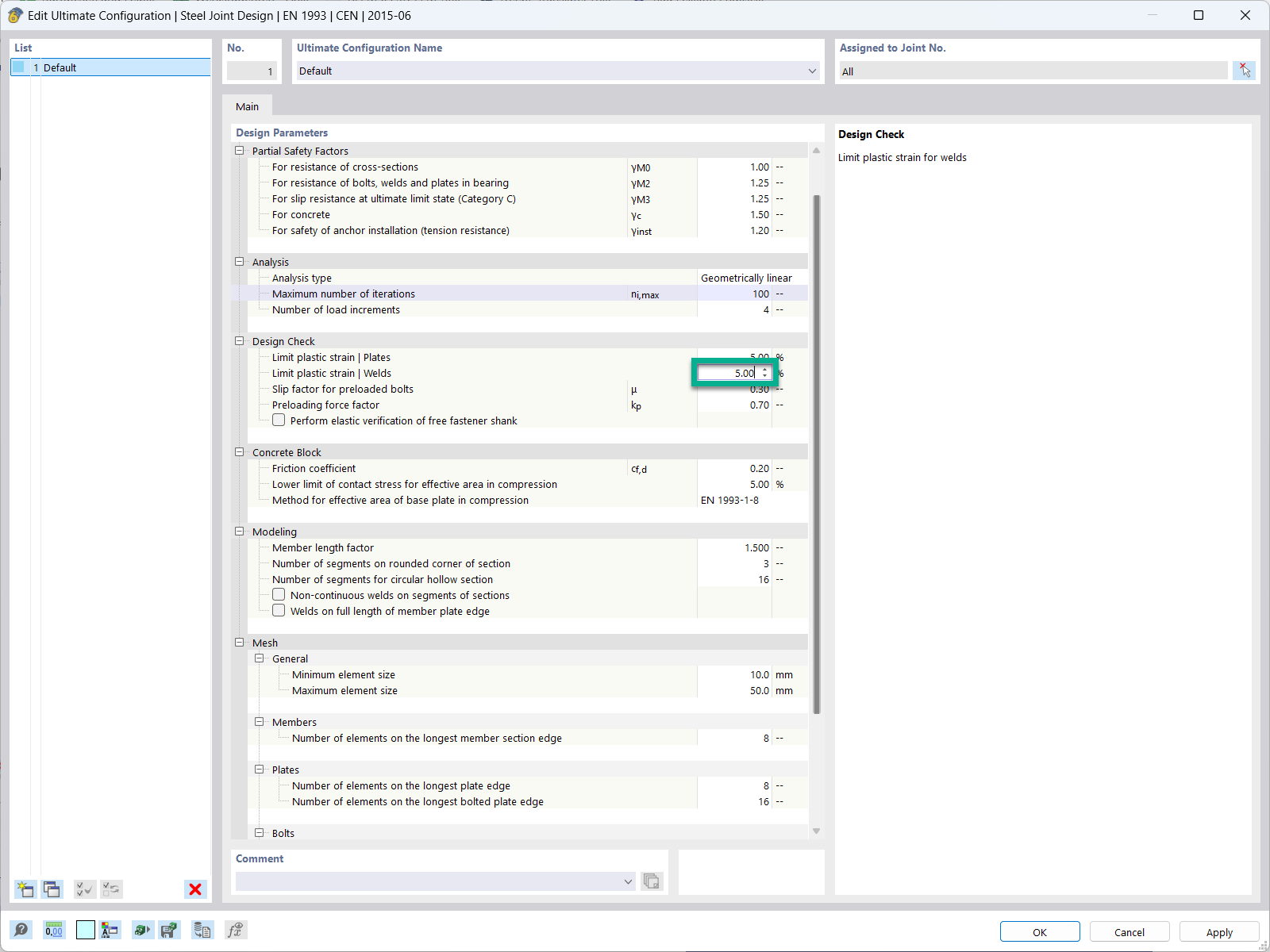
In the ultimate configuration of the steel joint design, you have the option to modify the limit plastic strain for welds.
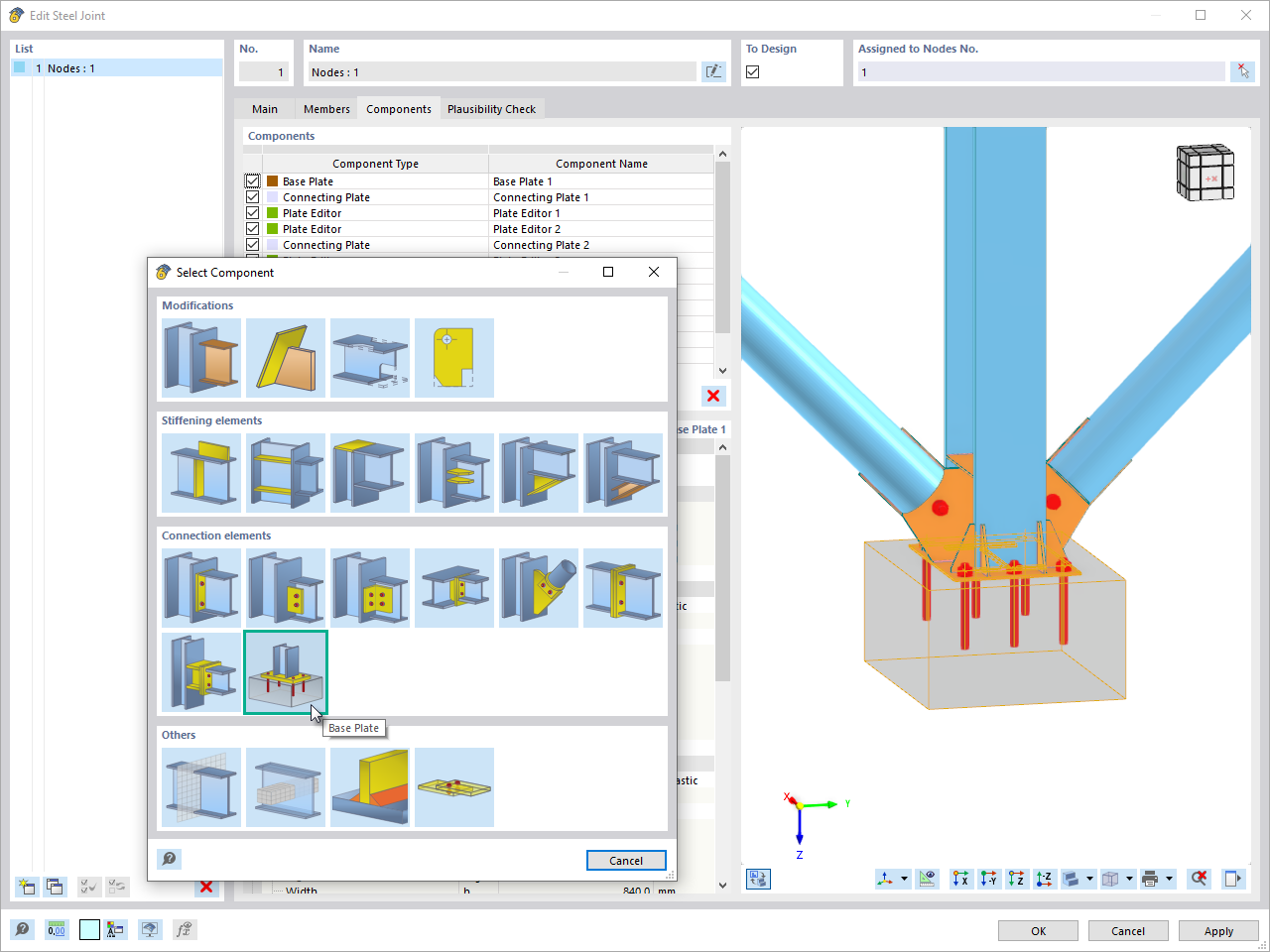
The "Base Plate" component allows you to design base plate connections with cast-in anchors. In this case, plates, welds, anchorages, and steel-concrete interaction are analyzed.
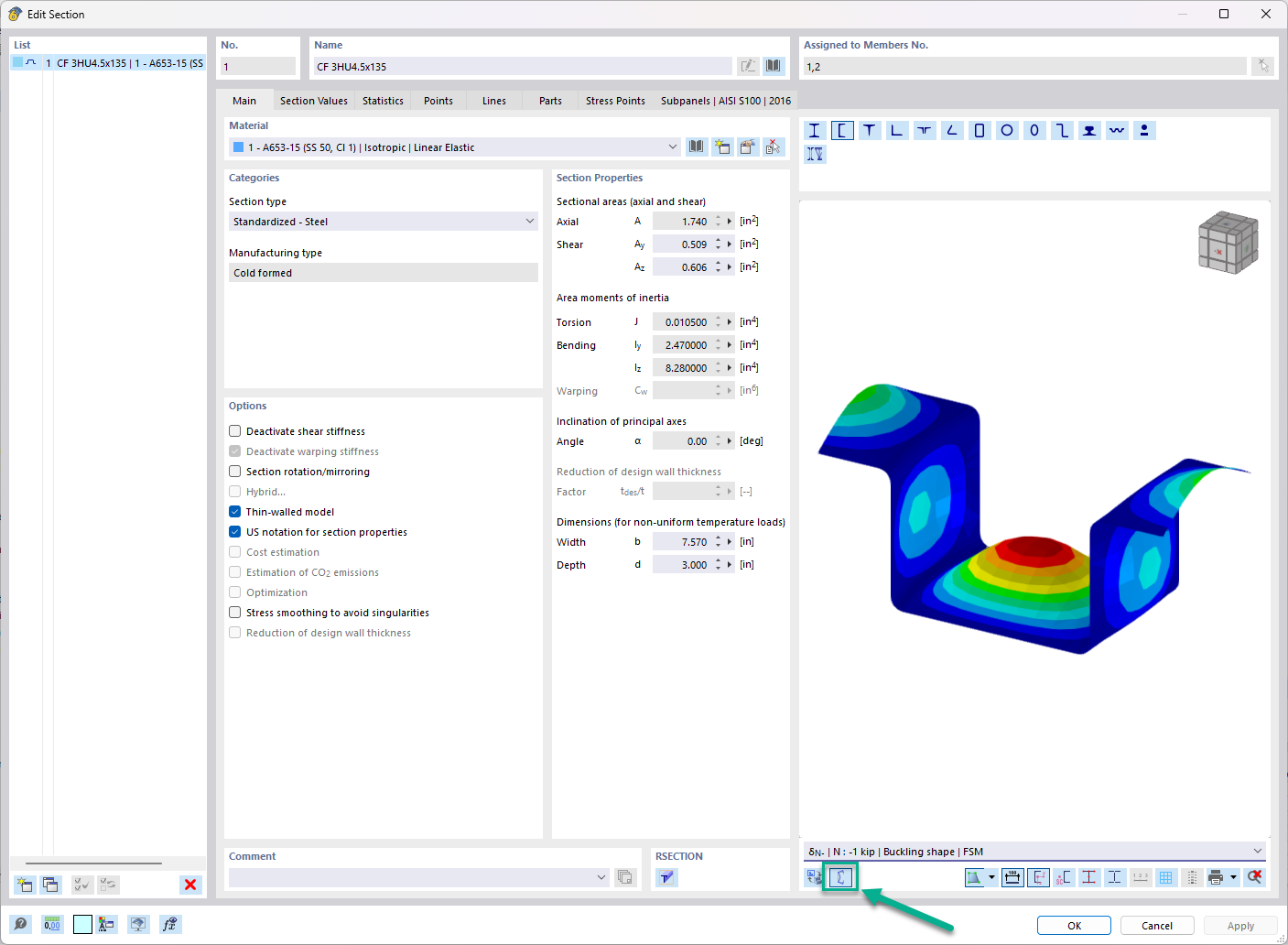
In the "Edit Section" dialog box, you can display the buckling shapes of the Finite Strip Method (FSM) as a 3D graphic.
In the Steel Joints add-on, I get high utilization ratios for preloaded bolts in the tension design. Where do these high utilization ratios come from and how can I evaluate the load-bearing reserves of the bolt?
How can treating a connection as fully rigid result in an uneconomical design?
Is it possible to consider shear panels and rotational restraints in the global calculation?