In September 2017, the Design Building at the University of Massachusetts in Amherst was completed. The $52 million project is one of the largest timber structures in the USA and one of the largest timber-concrete composite projects in the world.
The four-story university building, with a floor area of 87,500 ft², includes three faculties on the premises of UMass Amherst with offices, studios, lecture halls, and laboratories.
Investor
University of Massachusetts, Amherst, USA
www.umass.edu
Architectural Design
Leers Weinzapfel Associates Architects Boston, MA, USA
www.lwa-architects.com
Structural Design
Equilibrium Consulting Inc. Vancouver, BC, Canada
www.eqcanada.com
3D model (© Alex Schreyer / UMass)
The four-story university building, with a floor area of 87,500 ft², includes three faculties on the premises of UMass Amherst with offices, studios, lecture halls, and laboratories.
Investor
University of Massachusetts, Amherst, USA
www.umass.edu
Architectural Design
Leers Weinzapfel Associates Architects Boston, MA, USA
www.lwa-architects.com
Structural Design
Equilibrium Consulting Inc. Vancouver, BC, Canada
www.eqcanada.com
3D model (© Alex Schreyer / UMass)
Overall
This page has 0 user ratings.
5 star | ||
4 star | ||
3 star | ||
2 star | ||
1 star |
Steel Trusses and Timber-Concrete Composite Beams
No Download Possible
Customer Project / View Only
Number of Nodes | 83 |
Number of Lines | 153 |
Number of Members | 150 |
Number of Load Cases | 3 |
Number of Load Combinations | 3 |
Total Weight | 58.335 tons |
Dimensions (Metric) | 25.847 x 18.532 x 11.368 m |
Dimensions (Imperial) | 84.8 x 60.8 x 37.3 feet |
Program Version | 5.12.01 |

Very small torsional moments in the members to be designed often prevent certain design formats. In order to neglect them and still perform the designs, you can define a limit value in RF‑/STEEL EC3 from which torsional shear stresses are taken into account.

Structure stability is not a new phenomenon when referring to steel design. The Canadian steel design standard CSA S16 and the most recent 2019 release are no exception. Detailed stability requirements can be addressed with either the Simplified Stability Analysis Method in Clause 8.4.3 or, new to the 2019 standard, the Stability Effects in Elastic Analysis method provided in Annex O.

The RF‑/STEEL EC3 add-on module automatically transfers the buckling line to be used for the flexural buckling analysis for a cross-section from the cross-section properties. The assignment of the buckling line can be adjusted manually in the module input for general cross-sections in particular, as well as for special cases.

When optimizing cross-sections in the add-on modules, you can also select arbitrarily defined cross-section favorites lists - in addition to the cross-sections from the same cross-section series as the original cross-section.
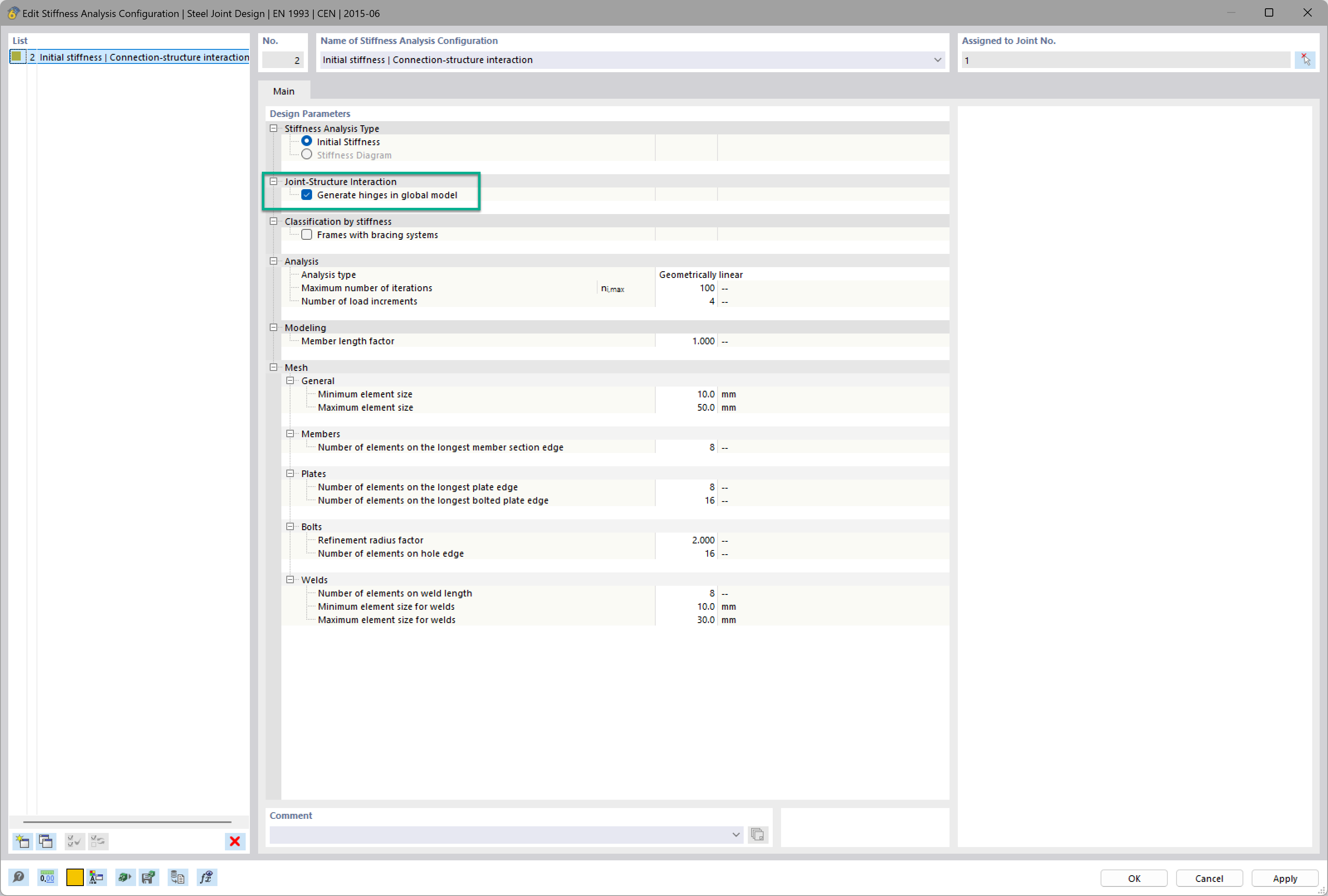
Want to automatically consider steel joint stiffness in your global RFEM model? Utilize the Steel Joints add-on!
Activate joint-structure interaction in the stiffness analysis of your steel joints. Hinges with springs are then automatically generated in the global model and included in subsequent calculations.
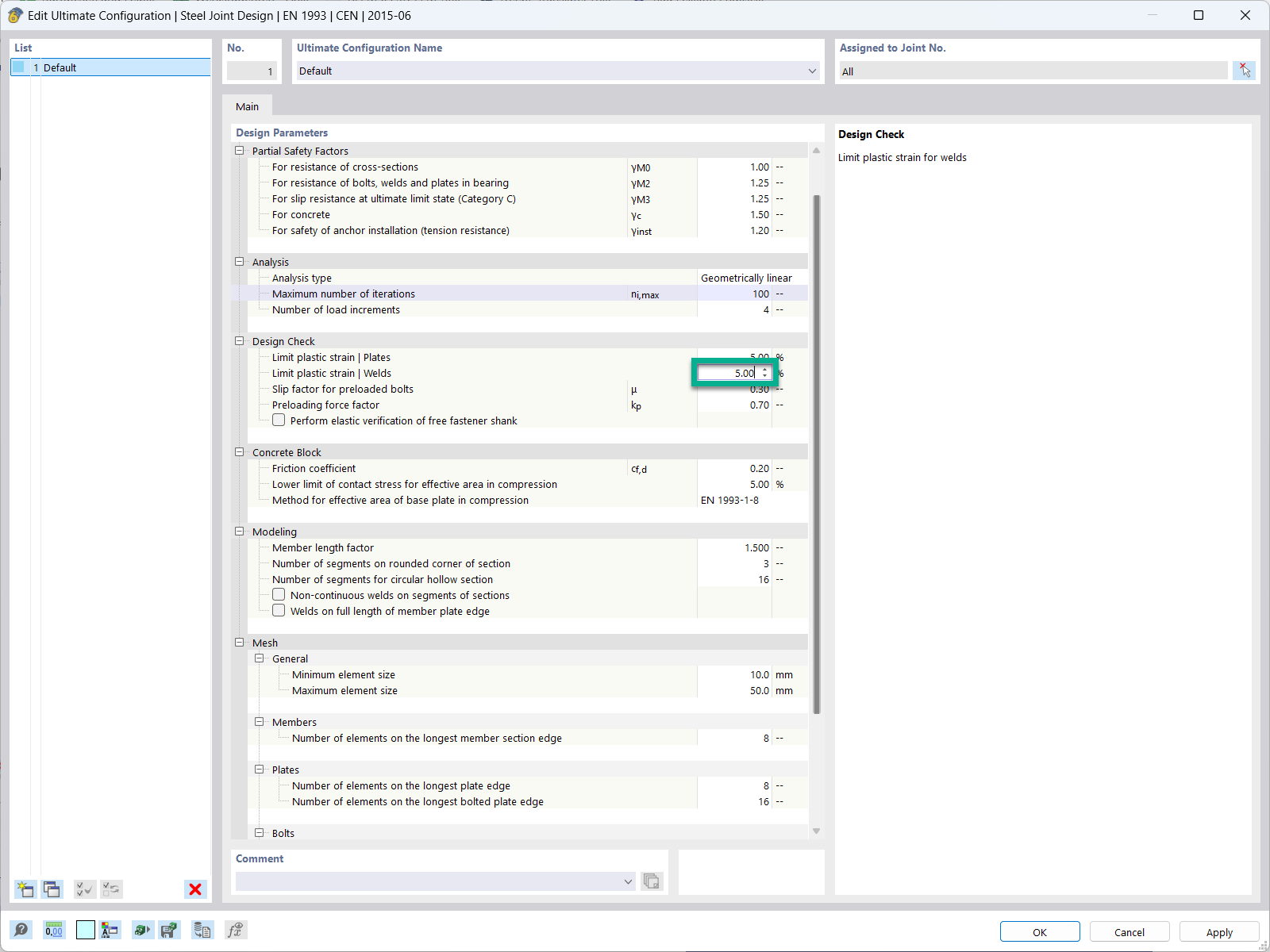
In the ultimate configuration of the steel joint design, you have the option to modify the limit plastic strain for welds.
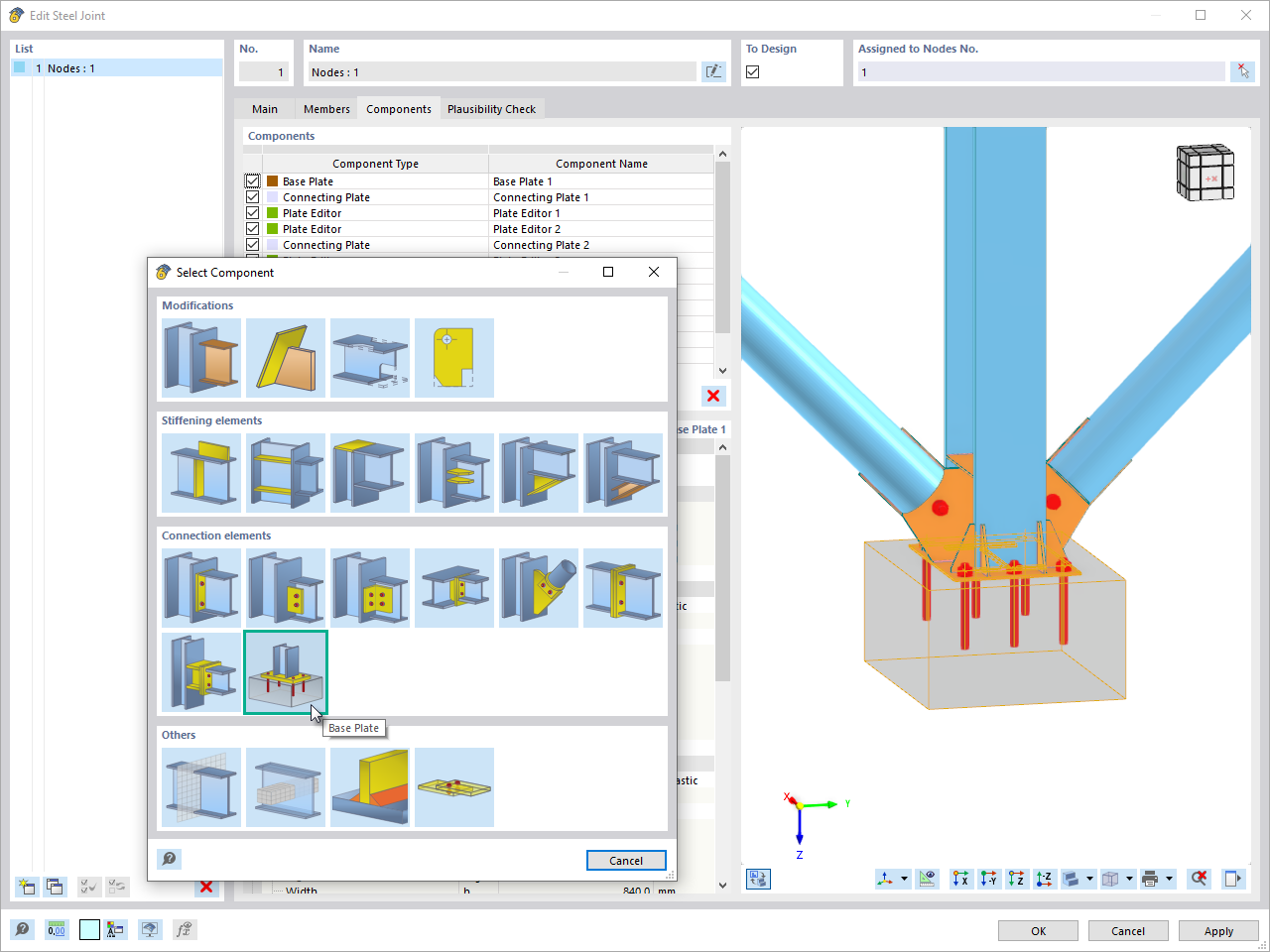
The "Base Plate" component allows you to design base plate connections with cast-in anchors. In this case, plates, welds, anchorages, and steel-concrete interaction are analyzed.
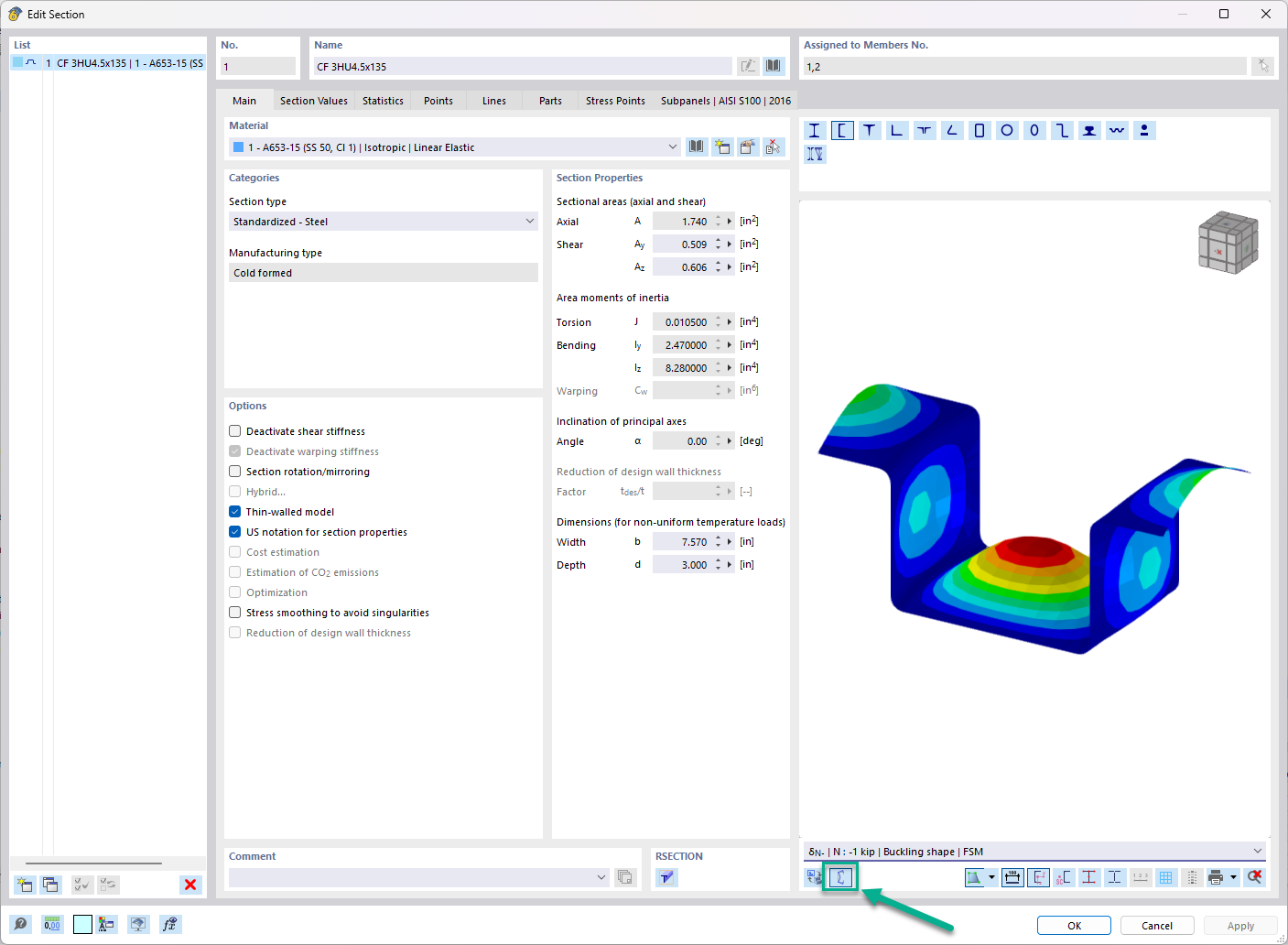
In the "Edit Section" dialog box, you can display the buckling shapes of the Finite Strip Method (FSM) as a 3D graphic.
What could be the reason?
Recommended Products for You