- Cross-section modeling using surfaces, openings, and point areas (reinforcements) limited by polygons
- Automatic or individual arrangement of stress points
- Extensible library of concrete, steel, and reinforcing steel materials
- Cross-section properties of reinforced concrete and composite cross-sections
- Stress analysis with yield hypothesis according to von Mises and Tresca
- Reinforced concrete design according to:
-
DIN 1045-1:2008-08
-
DIN 1045:1988-07
-
ÖNORM B 4700: 2001-06-01
-
EN 1992-1-1:2004
-
- For the design according to EN 1992-1-1:2004, the following National Annexes are available:
-
DIN EN 1992-1-1/NA:2013-04 (Germany)
-
NEN-EN 1992-1-1/NA:2011-11 (Netherlands)
-
CSN EN 1992-1-1/NA:2006-11 (Czech Republic)
-
ÖNORM B 1992-1-1:2011-12 (Austria)
-
UNE EN 1992-1-1/NA:2010-11 (Spain)
-
EN 1992-1-1 DK NA:2007-11 (Denmark)
-
SIST EN 1992-1-1:2005/A101:2006 (Slovenia)
-
NF EN 1992-1-1/NA:2007-03 (France)
-
STN EN 1992-1-1/NA:2008-06 (Slovakia)
-
SFS EN 1992-1-1/NA:2007-10 (Finland)
-
BS EN 1992-1-1:2004 (United Kingdom)
-
SS EN 1992-1-1/NA:2008-06 (Singapore)
-
NP EN 1992-1-1/NA:2010-02 (Portugal)
-
UNI EN 1992-1-1/NA:2007-07 (Italy)
-
SS EN 1992-1-1/NA:2008 (Sweden)
-
PN EN 1992-1-1/NA:2008-04 (Poland)
-
NBN EN 1992-1-1 ANB:2010 (Belgium)
-
NA to CYS EN 1992-1-1:2004/NA:2009 (Cyprus)
-
BDS EN 1992-1-1:2005/NA:2011 (Bulgaria)
-
LST EN 1992-1-1:2005/NA:2011 (Lithuania)
-
SR EN 1992-1-1:2004/NA:2008 (Romania)
-
- In addition to the National Annexes (NA) listed above, you can also define a specific NA, applying user‑defined limit values and parameters.
- Reinforced concrete design for stress-strain distribution, available safety, or direct design
- Results of reinforcement list and total reinforcement area
- Printout report with option to print a short form
SHAPE-MASSIVE | Features
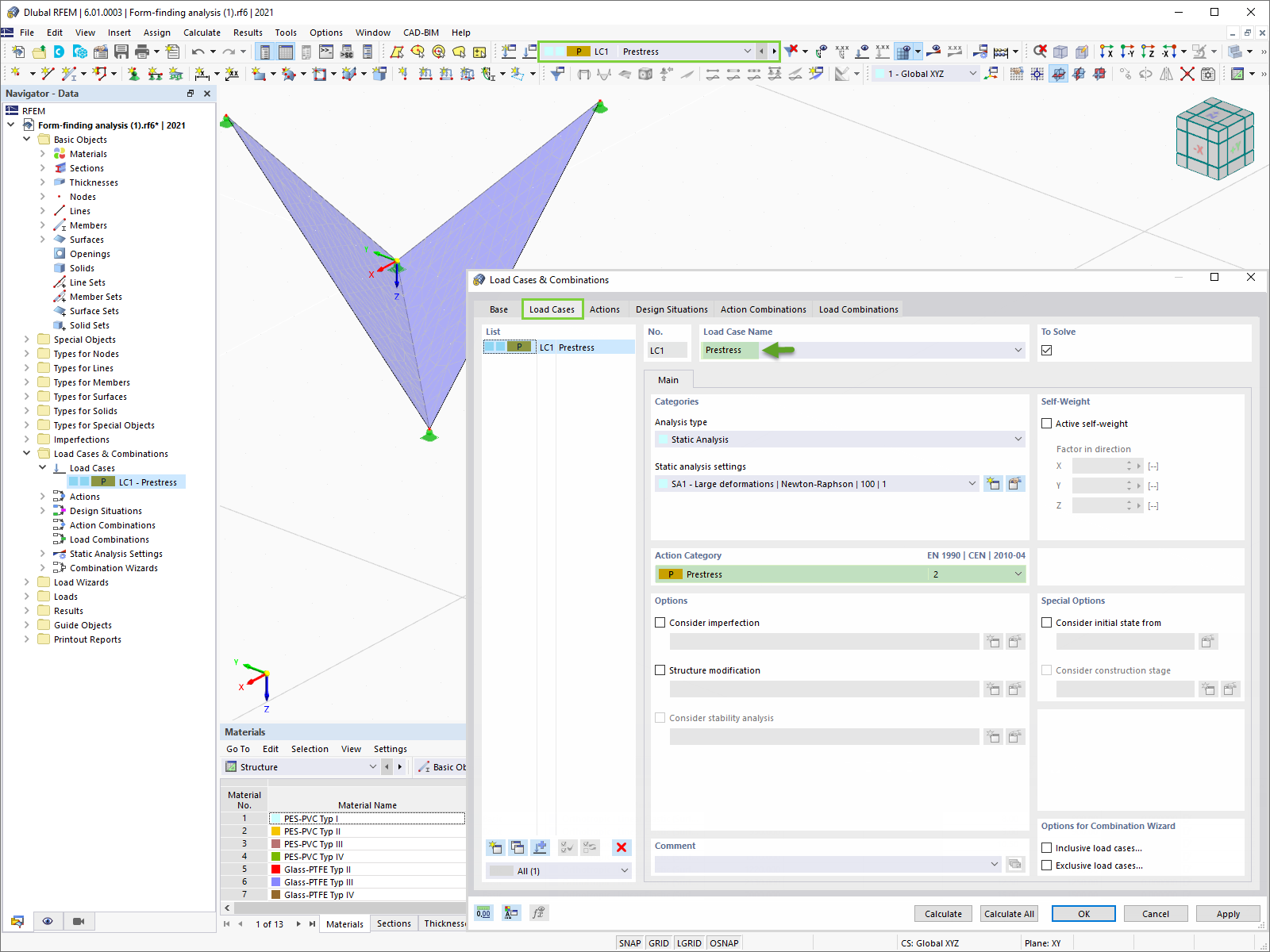
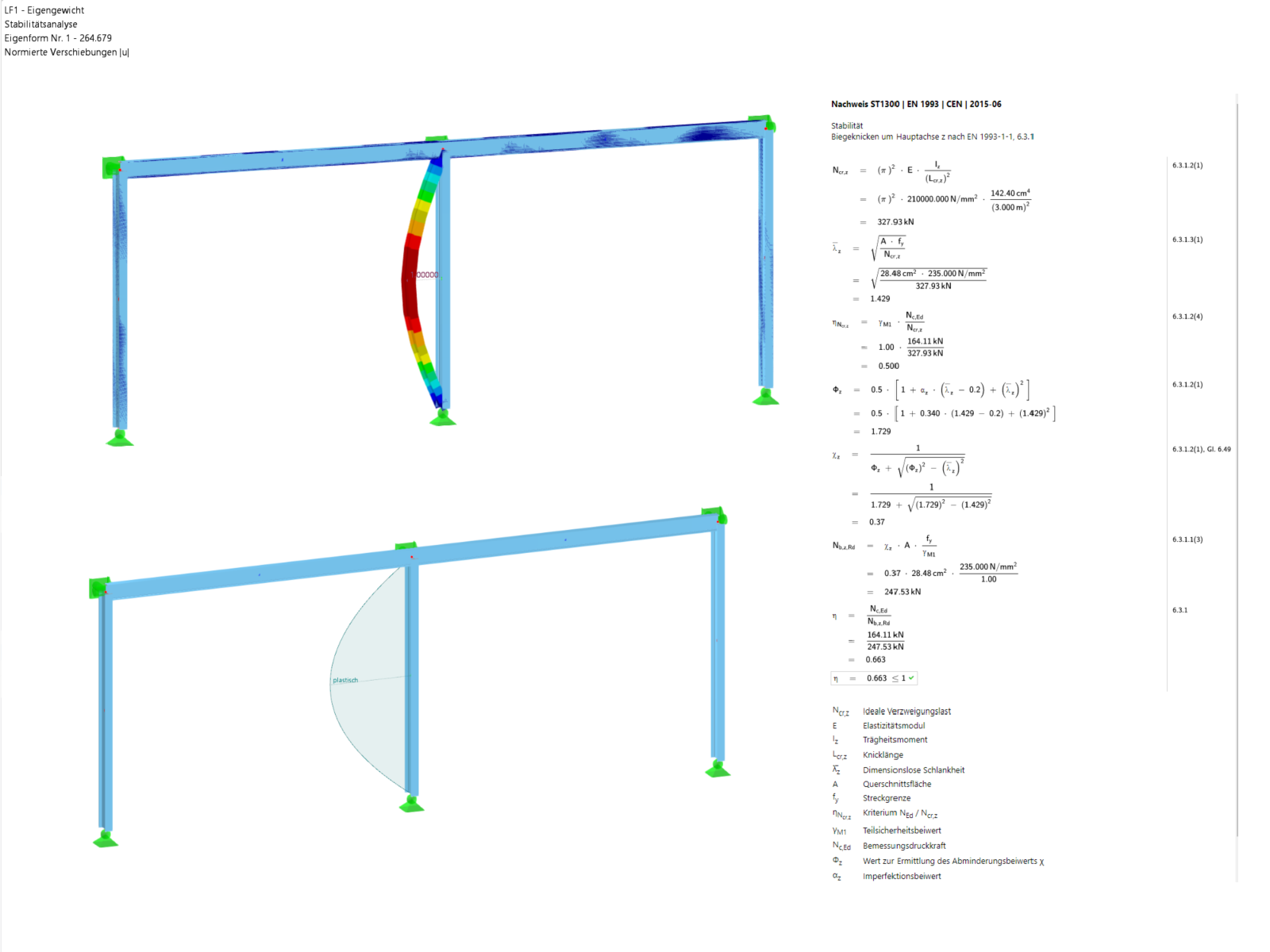
![Basic Shapes of Membrane Structures [1]](/en/webimage/009595/2419502/01-en-png-png.png?mw=512&hash=6ca63b32e8ca5da057de21c4f204d41103e6fe20)
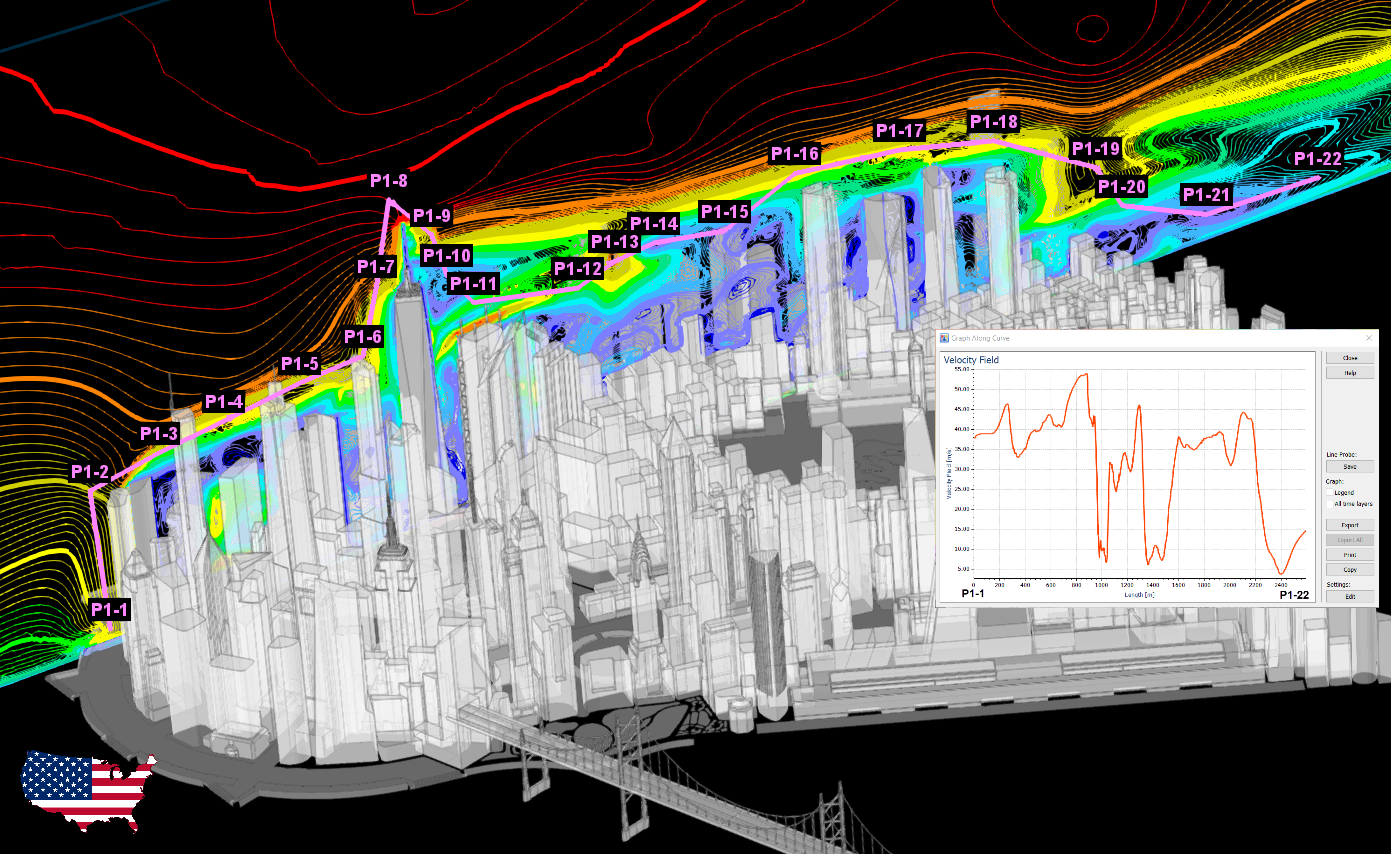
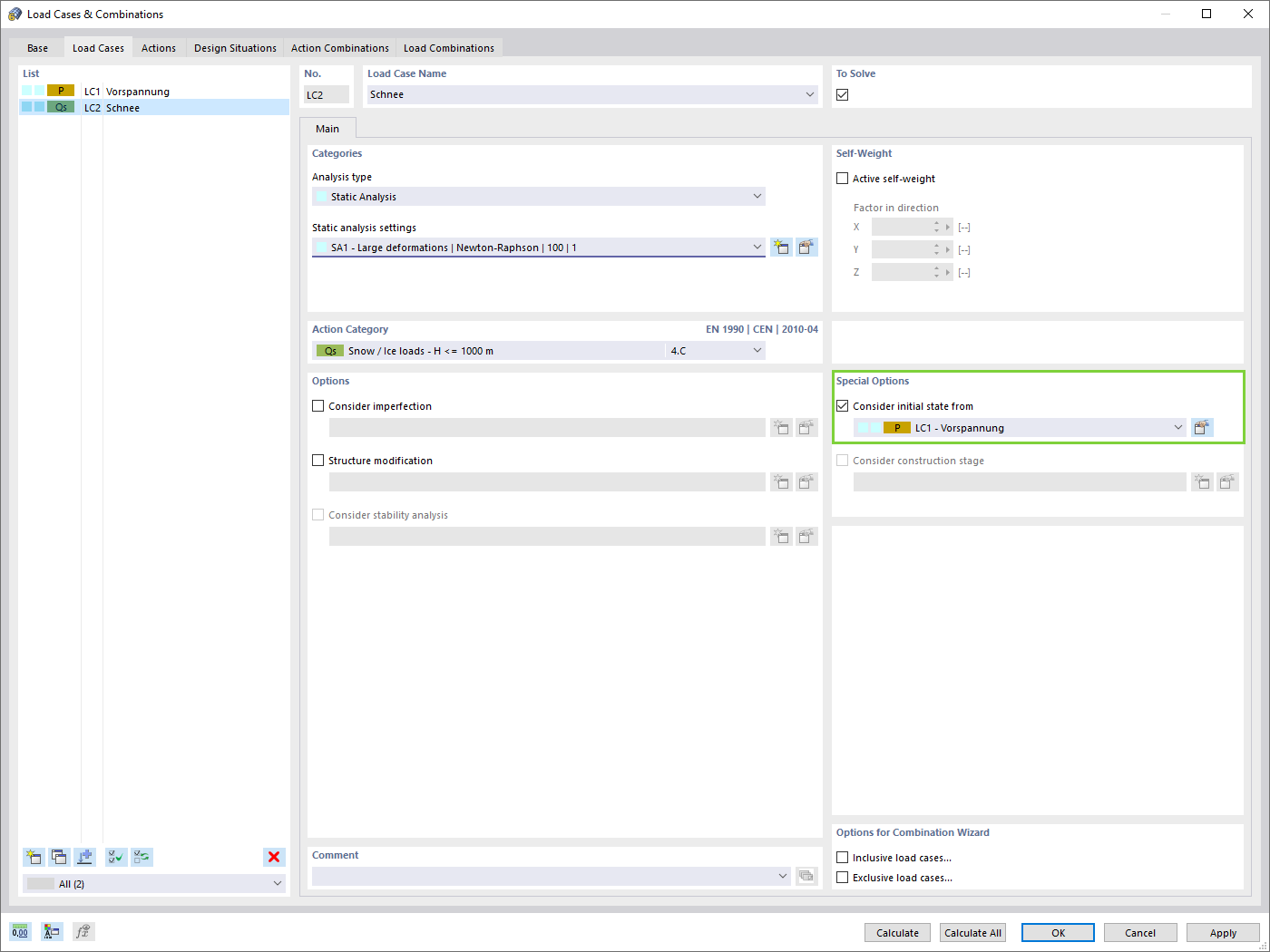
Compared to the RF-FORM-FINDING add-on module (RFEM 5), the following new features have been added to the Form-Finding add-on for RFEM 6:
- Specification of all form-finding load boundary conditions in one load case
- Storage of form-finding results as initial state for further model analysis
- Automatic assignment of the form-finding initial state via combination wizards to all load situations of a design situation
- Additional form-finding geometry boundary conditions for members (unstressed length, maximum vertical sag, low-point vertical sag)
- Additional form-finding load boundary conditions for members (maximum force in member, minimum force in member, horizontal tension component, tension at i-end, tension at j-end, minimum tension at i-end, minimum tension at j-end)
- Material types "Fabric" and "Foil" in material library
- Parallel form-findings in one model
- Simulation of sequentially building form-finding states in connection with the Construction Stages Analysis (CSA) add-on
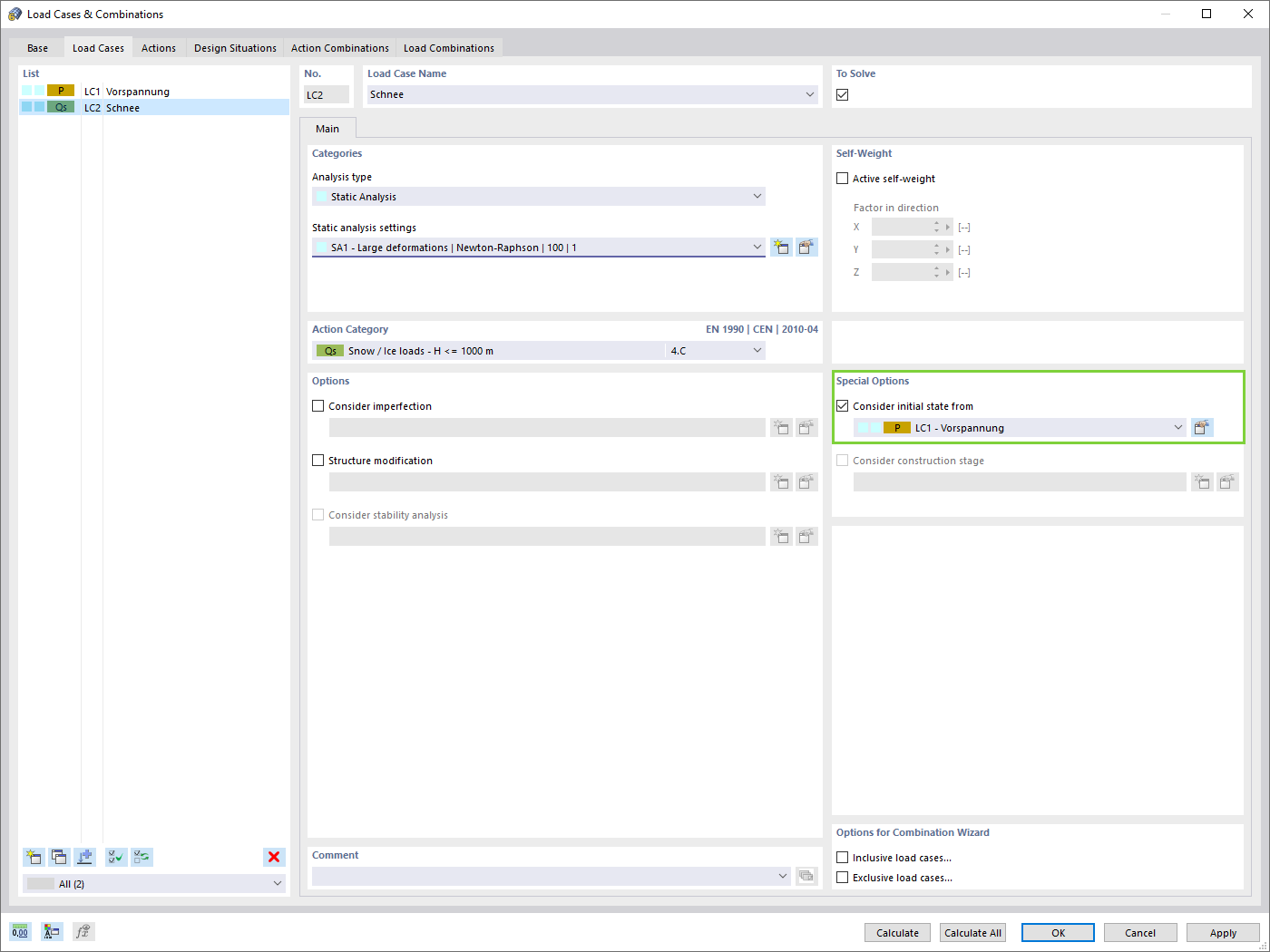
Do you know exactly how the form-finding is performed? First, the form-finding process of the load cases with the load case category "Prestress" shifts the initial mesh geometry to an optimally balanced position by means of iterative calculation loops. For this task, the program uses the Updated Reference Strategy (URS) method by Prof. Bletzinger and Prof. Ramm. This technology is characterized by equilibrium shapes that, after the calculation, comply almost exactly with the initially specified form-finding boundary conditions (sag, force, and prestress).
In addition to the pure description of the expected forces or sags on the elements to be formed, the integral approach of the URS also enables a consideration of regular forces. In the overall process, this allows, for example, for a description of the self-weight or a pneumatic pressure by means of corresponding element loads.
All these options give the calculation kernel the potential to calculate anticlastic and synclastic forms that are in an equilibrium of forces for planar or rotationally symmetric geometries. In order to be able to realistically implement both types individually or together in one environment, the calculation provide you with two ways to describe the form-finding force vectors:
- Tension method - description of the form-finding force vectors in space for planar geometries
- Projection method - description of the form-finding force vectors on a projection plane with fixation of the horizontal position for conical geometries
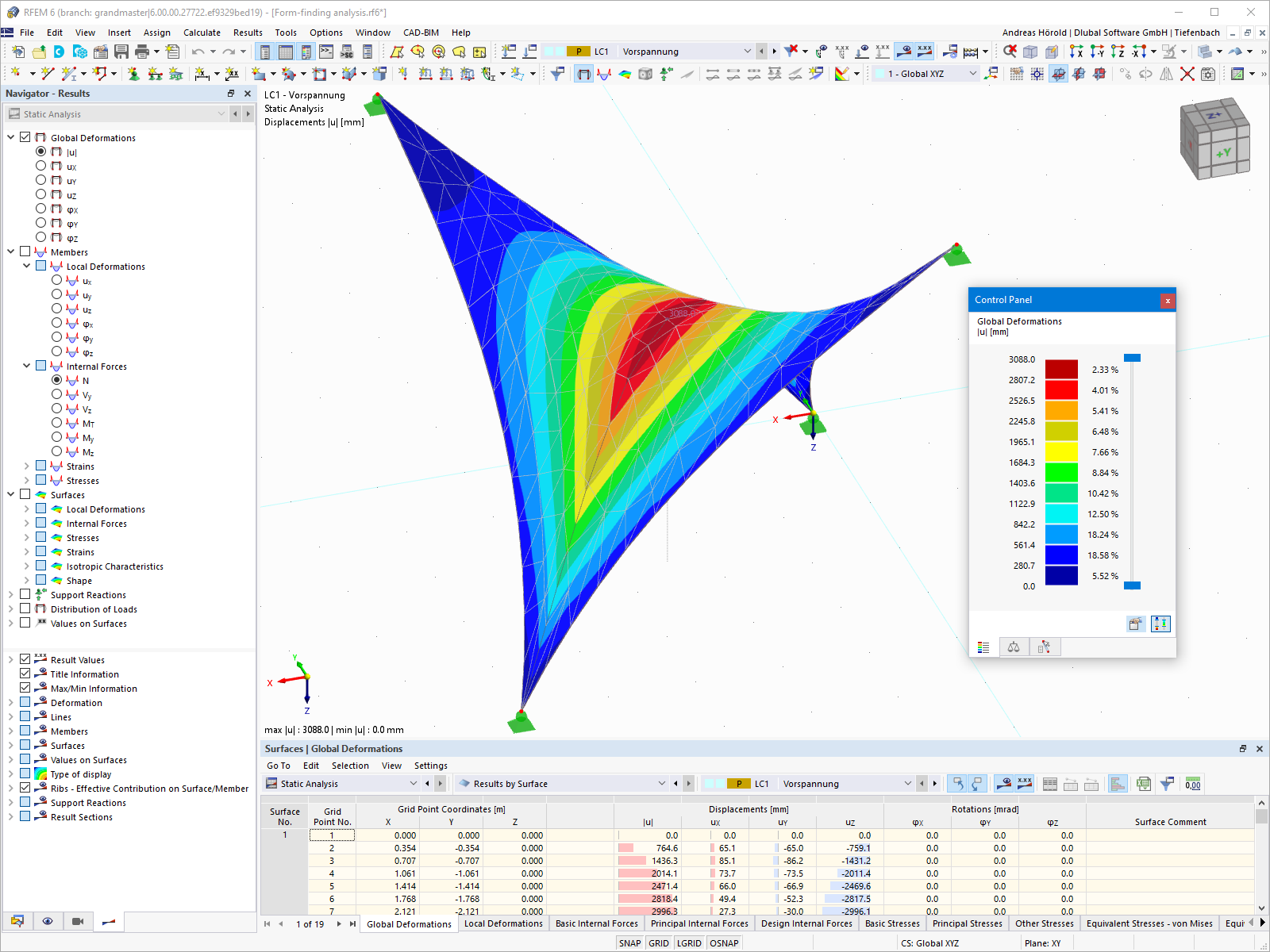
The form-finding process gives you a structural model with active forces in the "prestress load case" This load case shows the displacement from the initial input position to the form-found geometry in the deformation results. In the force or stress-based results (member and surface internal forces, solid stresses, gas pressures, and so on), it clarifies the state for maintaining the found form. For the analysis of the shape geometry, the program offers you a two-dimensional contour line plot with the output of the absolute height and an inclination plot for the visualization of the slope situation.
Now, a further calculation and structural analysis of the entire model is performed. For this purpose, the program transfers the form-found geometry including the element-wise strains into a universally applicable initial state. You can now use it in the load cases and load combinations.
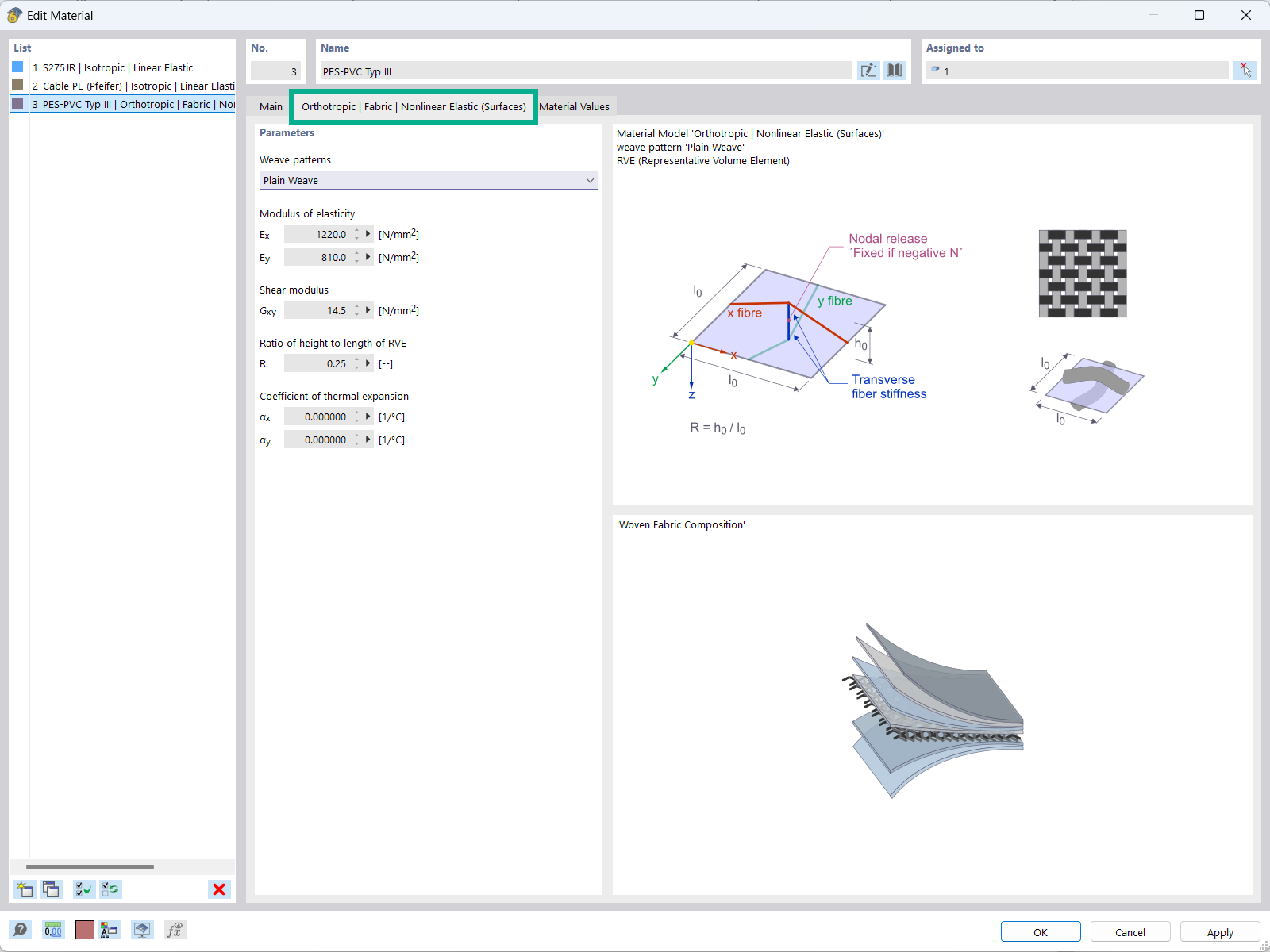
The "Orthotropic | Fabric | Nonlinear Elastic (Surfaces)" material model allows you to define prestressed fabric membranes using the representative microstructure-solid element model – RVE.
By considering the fabric geometry in the microstructure model, the corresponding transversal strain effect can now be considered for all force conditions in the membrane.
How do I create a user-defined fabric?
How can I fix the error warning “10060 - The structure is unstable” for modal analysis instability?